Ich habe mir zwei HF (Heeresfeldbahn) Hochbord- O- Wagen vom Typ MD 754 in 0n30 gedruckt. Vermutlich werden sich aber noch ein paar weitere Wagen dazu gesellen,
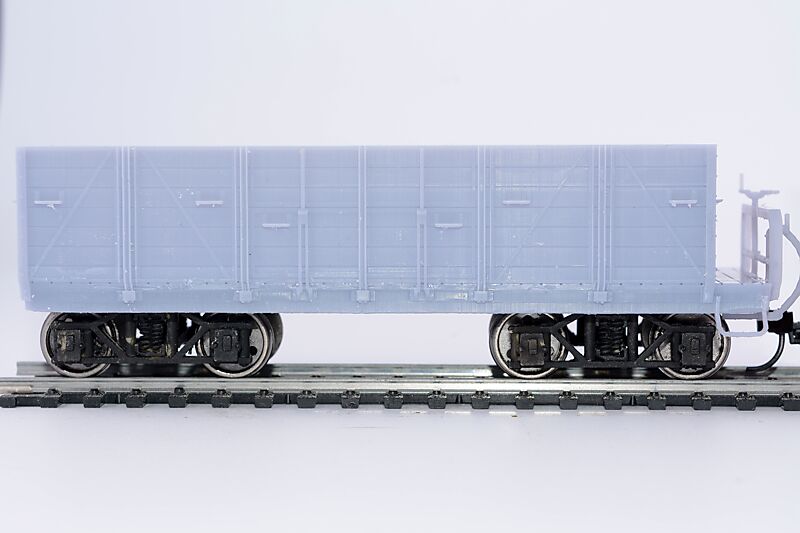
Die Dateien dazu sind eigentlich für H0e gedacht und wurden von Uwe Stehr erstellt. Man kann sie dankenswerterweise auf der Seite der Jagsttalbahn- Modelle kostenlos herunter laden. Dazu unter “FAHRZEUGE -> offene Güterwagen ->MD 754” nachschauen
Für mich habe ich die H0e Puffer entfernt (sehen in 0n30 recht klobig aus und stören die Kadee Kupplungen) und das Fahrzeug auf 1:48 hoch skaliert. In 1:45 ist der Wagen doch arg breit, breiter als Magic Train. Und das möchte ich weitestgehend verhindern. Da ich ja auch viele 0n30 Fahrzeuge habe, ist das überhaupt kein Problem.
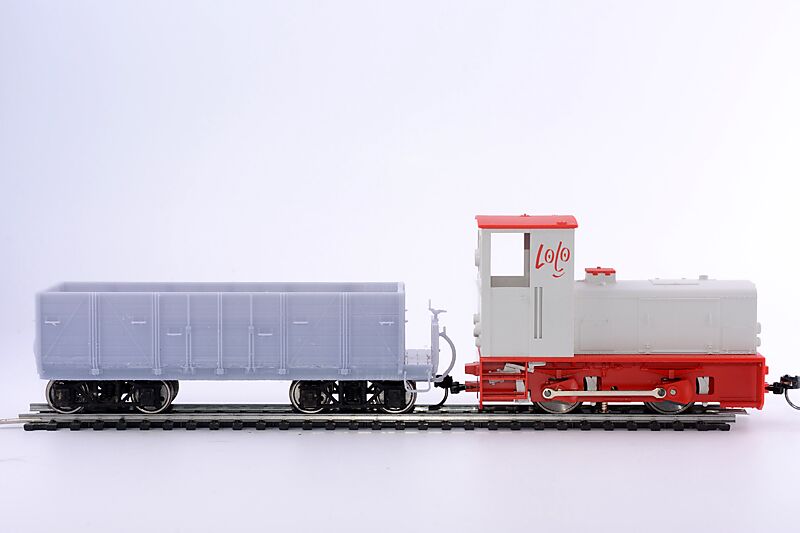
Aber auch zu Magic Train passen die Wagen von den Proportionen her prima. Sie sind jetzt nämlich exakt so breit wie der MT Diesel.
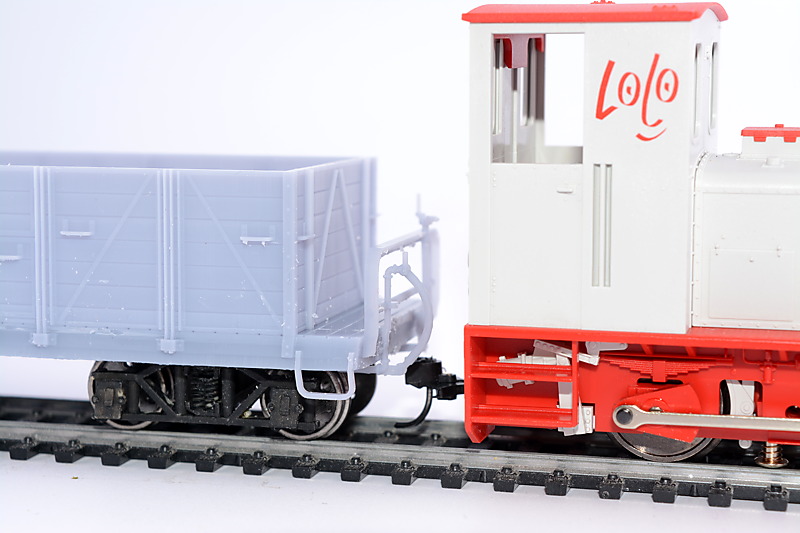
Der Detaillierungsgrad und die Filigranität ist, bedenkt man, das die Daten ja eigentlich für 1:87 und nicht 1:48 gedacht sind, erstaunlich. Da hat Uwe Stehr ganze Arbeit geleistet.
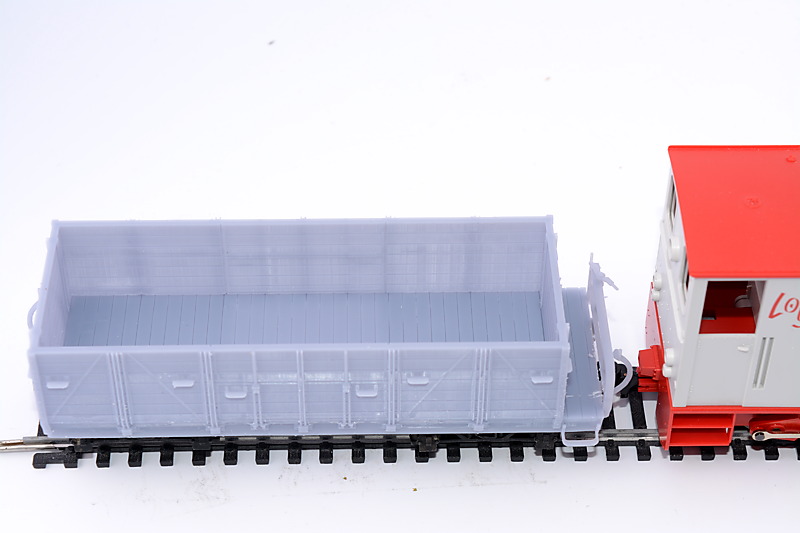
Die Bühne sieht zwar etwas kurz aus, ist aber exakt vorbildgetreu. In 1:48 müsste sie 10,1 mm lang sein, gemessen habe ich minimalst mehr als 10mm. Das passt also.
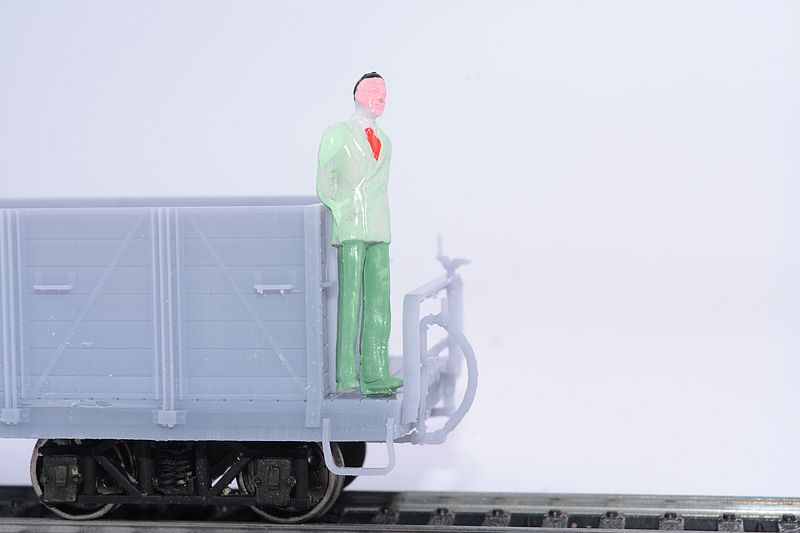
Aktuell habe ich noch keine Drehgestelle für die Wagen. Deswegen ruhen sie zur Zeit noch auf meinen Diamond- Drehgestellen. Die mitgelieferten HF Drehgestelle lassen sich leider nicht so einfach auf 1:48 bzw. 1:45 hoch skalieren. Irgendwann werde ich mal entsprechende Blenden für das Diamonds- Skript entwickeln, damit meine Wagen auch passende Drehgestelle bekommen. Das ist aber noch lange nicht so weit.
Derweil habe ich mir doch auch mal die mitgelieferten Drehgestelle angesehen. Zum Glück sind die STL- Dateien dafür, im Gegensatz zu den Dateien für den eigentlichen Wagen, “waterproof” und lassen sich somit in OpenSCAD weiter verarbeiten.
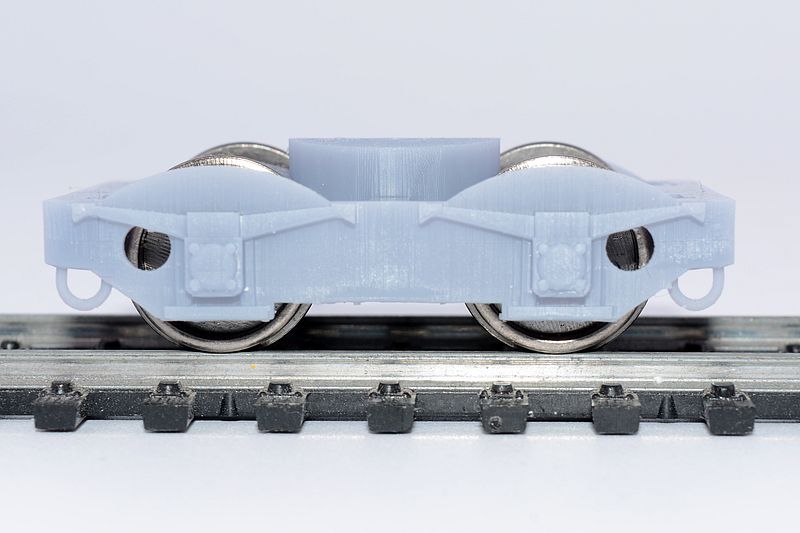
Also habe ich die Drehgestelle skaliert und dort die Spitzenlagerung eingebaut, die sich schon bei den Diamonds bewährt hat.. Allerdings it der erste Versuch dann doch zu breit geworden. Die dafür eigentlich vorgesehenen Roco H0 Radsätze mit 10,4 mm Rädern und 24,75 mm Achsen fallen einfach durch. Zur Zeit druckt eine schmalere Version, die dann hoffentlich passt. Bei den schon fertigen sind sogar die Hornby Radsätze mit 26mm Achsen noch zu kurz. Aber für ein erstes Foto reicht es dann doch.
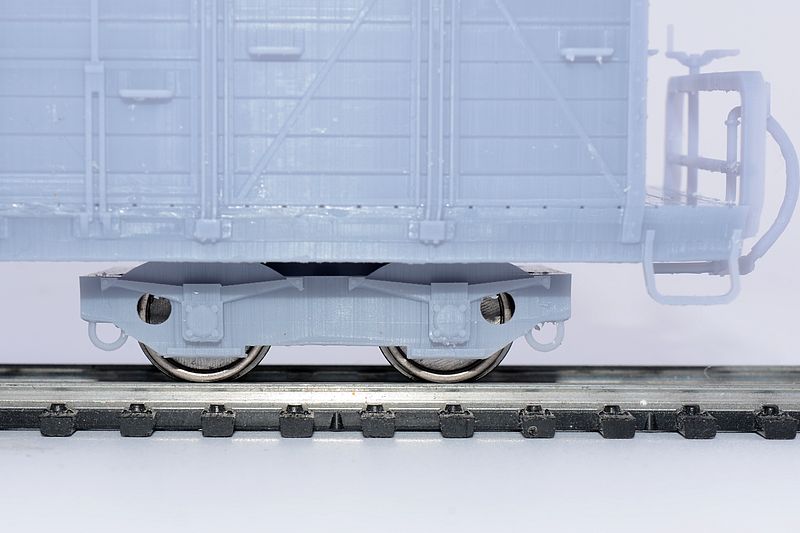
Auch wenn es sich eigentlich um den “anderen” Drehgestell- Typ handelt als der, der aktuell unter dem ja immer noch existierenden Wagen sitzt, handelt es sich doch eindeutig um HF Drehgestelle.
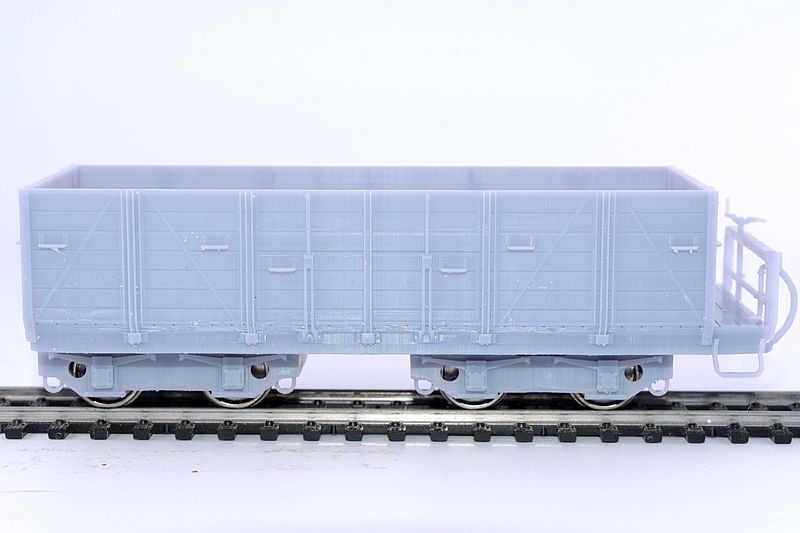
Die Drehgestelle liegen nur lose unter dem Wagenkasten. Dennoch ist der Gesamt- Eindruck so erheblich besser als mit den nicht so wirklich passenden Diamond Drehgestellen.
Wenn die Breite der Drehgestelle dann passt, kann ich die Wagen lackieren und die Drehgestelle sowie Kupplungen anschrauben. Dann ist alles so weit fertig. Ich weiß noch nicht, ob ich die geänderten STL Dateien hier veröffentlichen darf. Wenn ich das in Erfahrung gebracht und die Genehmigung bekommen habe, gibt es die entsprechenden STL Dateien wie gewohnt zum Download. Schließlich habe ich ja kaum etwas an den Dateien verändert, außer sie zu skalieren.
Inzwischen ist der zweite Satz Drehgestelle fertig und nun passen die Roco Radsätze genau rein.
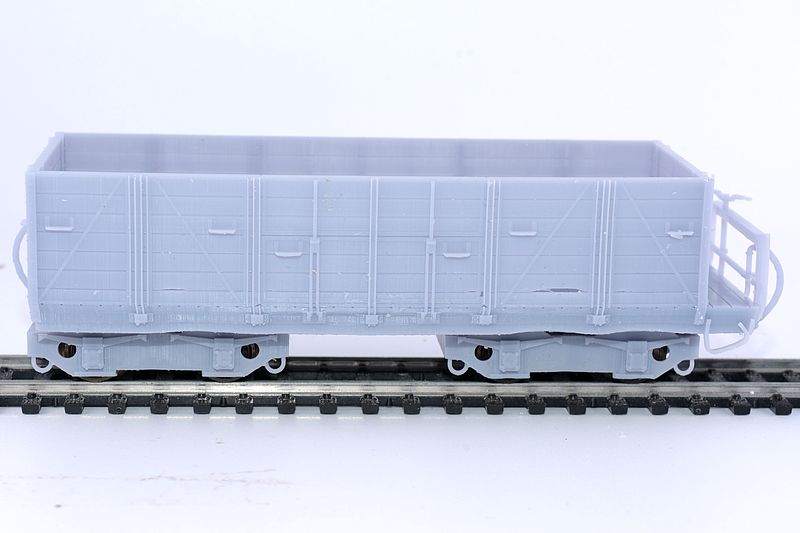
Angeschraubt sind die Drehgestelle noch nicht, da ich keine passenden Schrauben vorrätig habe. Die 1,5 – 1,7 mm dicken (eher dünnen) selbst schneidenden Schrauben müssen mindestens 10mm lang sein. Die längsten Mini- Schrauben aus meinem Bestand sind aber nur 6 mm. Alles, was 10mm hat, ist zu dick. Damit die Position aber für die Fotos erst mal stimmt, habe ich je einen Schienennagel durchgesteckt Somit sitzen die Drehgestelle, wo sie sitzen sollen. Ich habe auf die Schnelle keine 10,4mm Radsätze zur Hand gehabt. Deswegen sind 11 mm Räder mit einer 24,75mm langen Achse drin. Das ist auf jeden Fall noch vorbildgetreu und entspricht den größeren 500 mm Rädern des Vorbilds. Genau wären das dann 11,1 mm. Das eine Zehntel spielt gar keine Rolle. Die kleineren 450 mm Räder des Vorbilds entsprechen dann 10 mm Rädern…
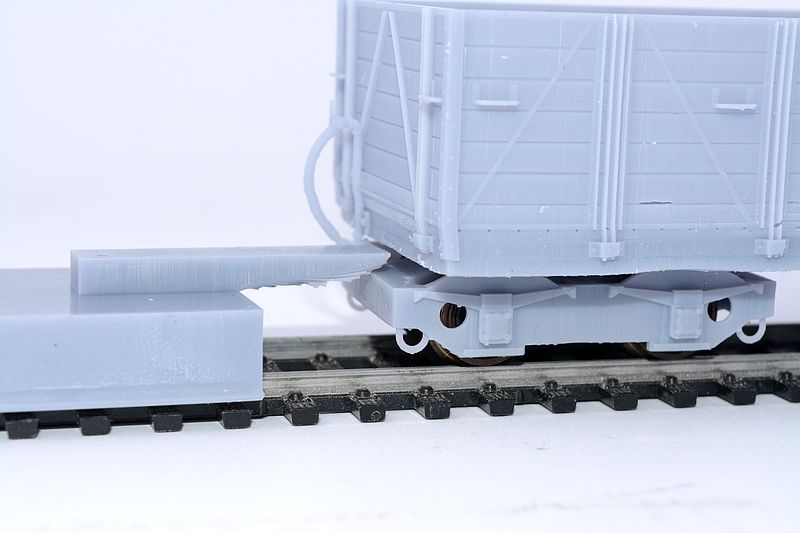
Wenn ich die Rad- Größe beibehalte, muss ich die Gearboxen für die Kadee Kupplungen leicht unterfüttern. Die Oberkante der Schablone muss genau mit der Oberkante der Gearbox zusammenpassen. Auf dieser Seite ist wohl gar nicht genug Platz für eine Standard- Gearbox von Kadee. Muss mal sehen, was ich da hin fummeln kann… Auf der anderen Seite ist wegen der Bremserbühne mehr Platz…
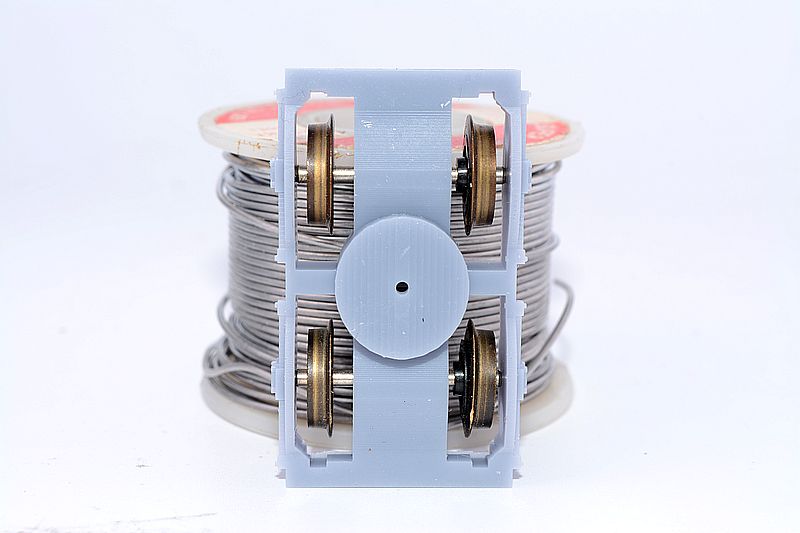
Die Radsätze werden einfach von unten in die Drehgestelle eingefädelt, wie meistens.
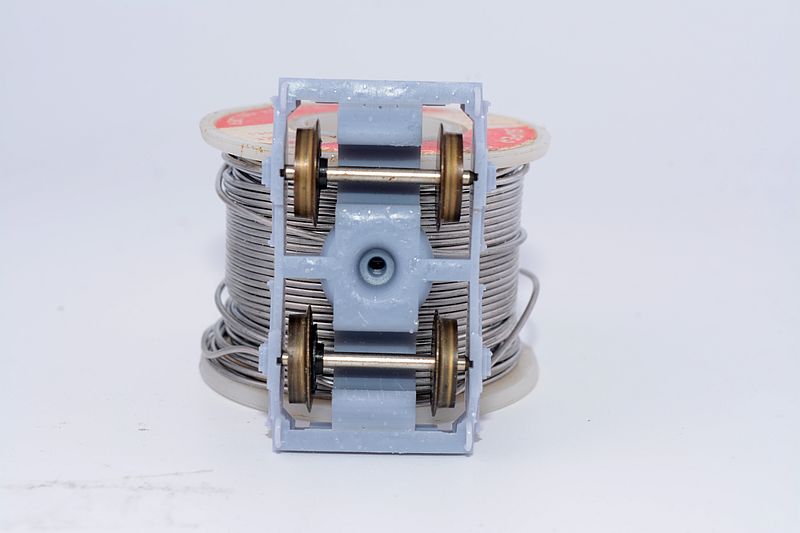
Die Unterseite ist mit Stützmaterial gedruckt worden. da man diese Drehgestelle nicht flach auf das Druckbett setzen kann. Dadurch ist die Optik hier nicht so schön. Das sieht man aber normalerweise nicht. Mindestens einer der Radsätze auf dem Foto ist Schrott. Sind halt 40 Jahre alte ausgelutschte H0 Radsätze. Für den “echten” Einsatz kommen da neue RP25 Räder rein. Zum Ausprobieren geht es aber auch erst mal so.
Auf der Seite der Jagsttalbahn- Modelle gibt es noch viele weitere Datensätze zum kostenlosen Download. Als nächstes “Opfer” habe ich mir den MD 435 ausgesucht, ebenfalls ein HF Wagen, allerdings als Niederbordwagen.
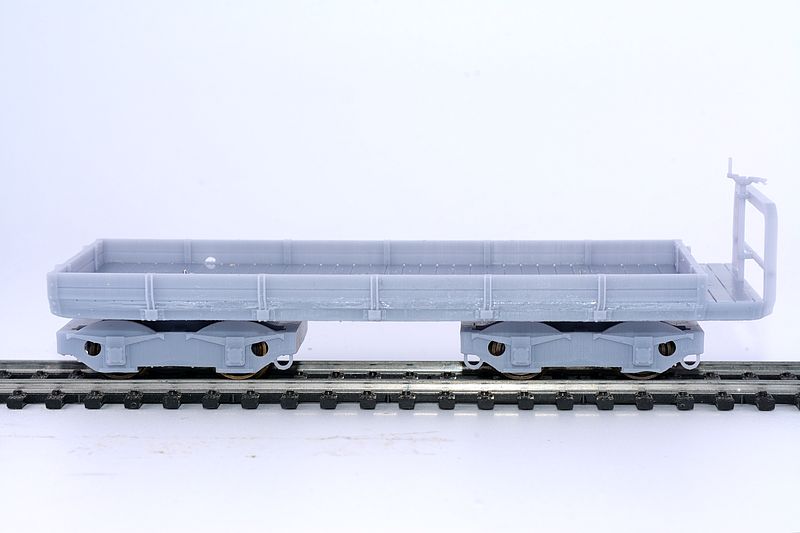
Auch hier habe ich den im Original für H0e gedachten Datensatz auf 1:48 hoch skaliert und die “angespritzten” Puffer entfernt.
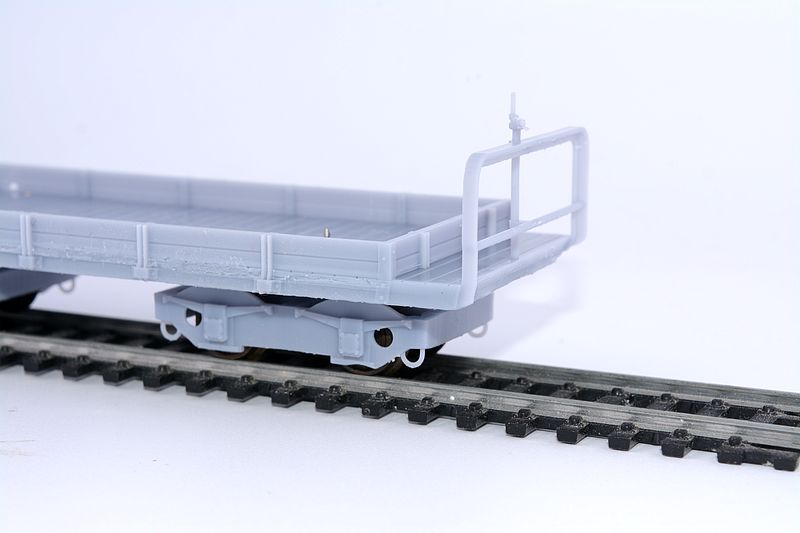
Die Drehgestelle sind dieselben HF Drehgestelle wie auch beim MD 754. Und auch hier sind wieder statt eine Schraube ein Schienenagel zur Positionierung der Drehgestelle verwendet worden. Ich habe inzwischen aber passende Schrauben gefunden und bestellt. Sie sollten in ein paar Tagen ankommen.
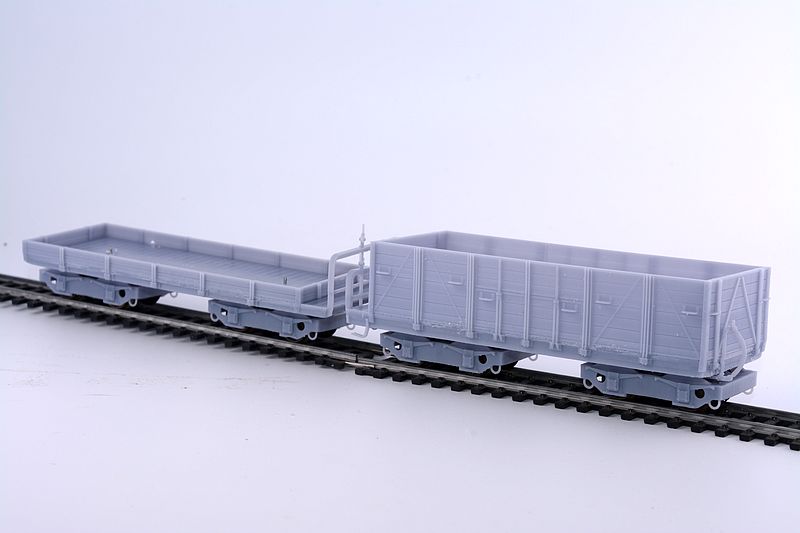
Und so macht der “Neue” sich im Verbund mit dem “Alten”…
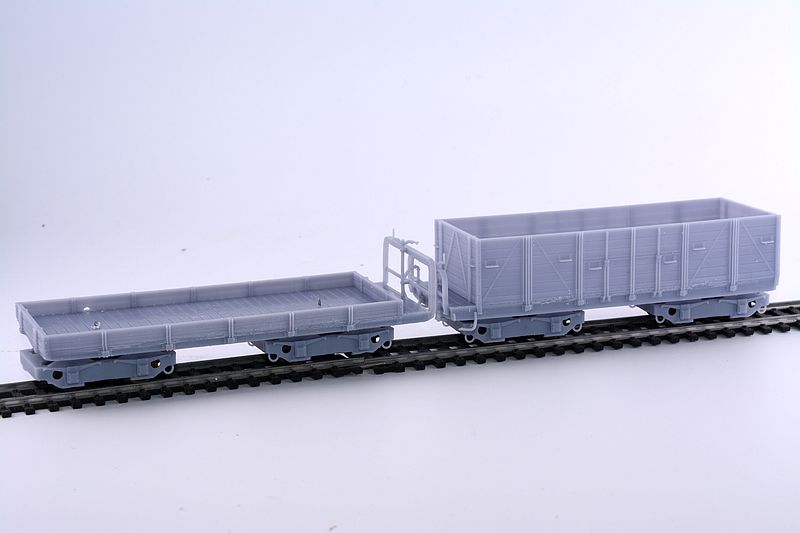
Beim MD 435 ist das Geländer an der Bühne erheblich höher. Ich weiß aber nicht, ob das bei beiden Wagen so vorbildgetreu ist oder ob der MD 754 da einen Fehler aufweist.
Aus dieser Serie von HF Wagen gibt es noch mehr Wagen. Ich finde diese Wagen trotz ihrer problematischen Herkunft (sie sind ja in beiden Weltkriegen fürs Militär konstruiert und gebaut worden) ziemlich interessant. Vierachser, also dank Drehgestellen gute Laufeigenschaften und dabei kaum länger als die MT Zweiachser.
Als nächstes aus dieser Serie ist der MD 419 geplant, ein geschlossener Wagen mit ganz ähnlichen Abmessungen, außer in der Breite. Eigentlich ist dieser Wagen selbst in 1:48 mit knapp 54mm zu breit für mein selbst gestecktes Limit von 50mm Aber ich wollte ihn jetzt nicht noch kleiner machen, damit er zu den anderen Wagen passt. Und 1:48 ist ja einer der Standart- Maßstäbe in Spur 0, von daher…
Es wird aber wohl noch 1-2 Tage dauern, bevor ich ihn drucke. Denn seit heute bin ich nicht mehr Krank geschrieben und muss “nebenbei” wieder “etwas” arbeiten.
Inzwischen habe ich auch ein Exemplar des MD-419 gedruckt.
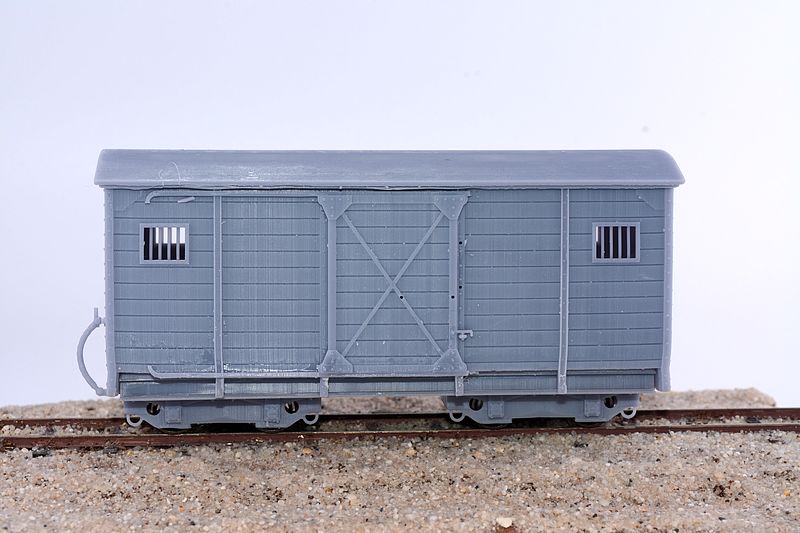
Die Detaillierung dieser eigentlich für H0 gedachten Datensätze ist schier unglaublich, finde ich. Da fehlt mir in 0 wirklich gar nichts. Mir gefallen die G- Wagen sogar noch besser als die O- Wagen.

Der Wagen besteht aus zwei Teilen, dem Chassis und dem Aufbau. Das erleichtert die Lackierung doch erheblich. Allerdings wird viel Stützmaterial und damit auch viel Harz verbraucht. Und auch bei diesen Wagen weiß ich noch nicht, was ich mit den Kupplungen machen soll. Die normale Kadee Gearbox passt nicht, weil sie mit den Drehgestellen kollidiert. Vielleicht kann man einen NEM Schacht an die Drehgestelle bauen. Das muss ich mal als nächstes testen Oder irgendwie die Gearbox quasi vor die Pufferbohle setzen. In die Pufferbohle geht nicht, weil sie dann zu hoch wäre.
Ich denke aber, ich habe eine einfache Lösung für das Kupplungsproblem gefunden. Ich drucke einen NEM Schacht, der entsprechend abgesenkt an die Pufferbohle geklebt wird. Der NEM 362 Schacht sitzt ja tiefer als eine typische 0e Pufferbohle. Dadurch steht er vor und ist den Drehgestellen nicht im Weg. Für den NEM Schacht gibt es für fast jedes in 0e gebräuchliche Kupplungssystem eine Lösung. Für mich eben Kadee No#18. So sieht das Ganze dann aus, zumindest in der Konstruktion.
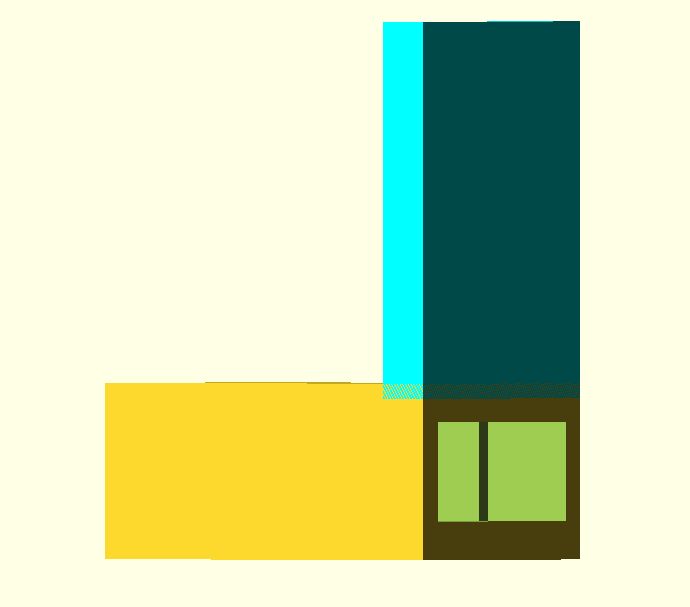
Es gibt auch eine Variante mit einem zusätzlichen (im Skript einstellbaren) Abstandsstück. Bei einigen der HF Wagen stehen die Drehgestelle ja sogar ein gutes Stück über die Wagenkästen hinaus.
Um die genaue Höhe einstellen zu können, habe ich, ganz ähnlich der Hilfe für Kadee Gearboxen auch eine Justierhilfe für NEM 362 Schächte konstruiert.
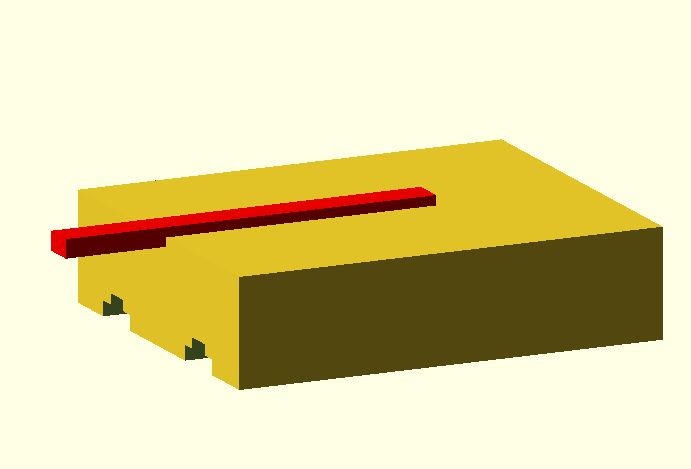
Und in “echt”, frisch gedruckt dann so:
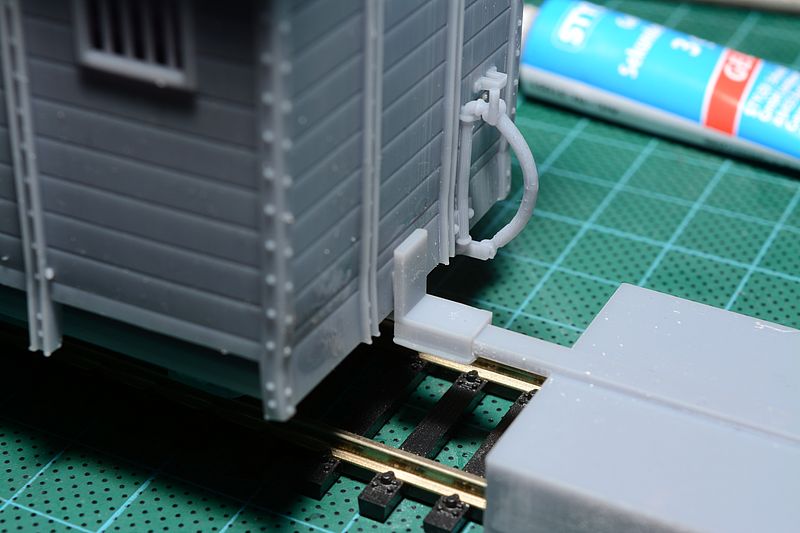
Ich kann die Teile grade nicht ankleben, weil ich eine frische Tube Kleber aus der Tiefkühltruhe geholt habe, der jetzt erst “auftauen” muss. Ist zwar nicht schön, aber zumindest funktional.
Um die Zwangspause beim Drucken zu nutzen, habe ich angefangen, die G-Wagen zu lackieren, da ich hier keine neuen Aufbauten drucken muss. Hier müssen nur die Drehgestelle anders werden.
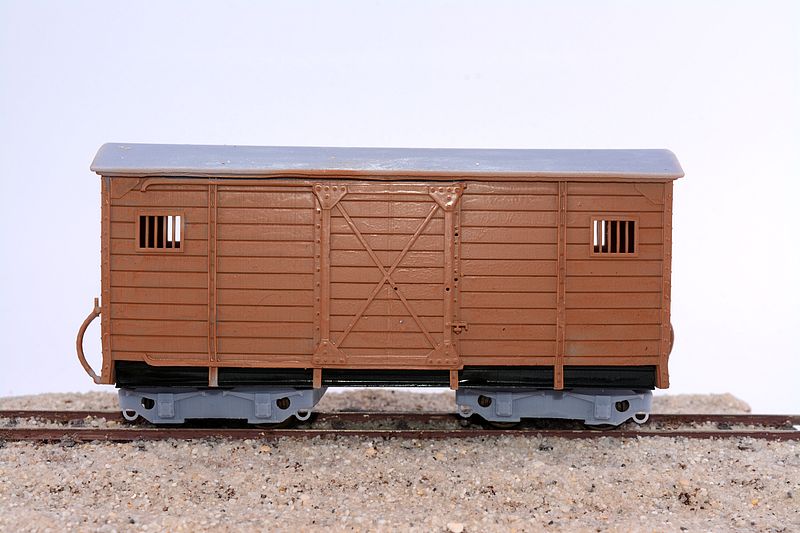
Ich habe für den Aufbau “Mud Brown” von Vallejo Model Air verwendet. Ist etwas heller als das typische Güterwagenbraun, stört mich aber nicht, im Gegenteil. Die Fahrwerke sind einfach Schwarz. Die Drehgestelle sollen auch schwarz werden, wenn ich denn die “Richtigen” habe drucken können. Aktuell liegt der Wagen nur lose auf den alten Drehgestellen auf.
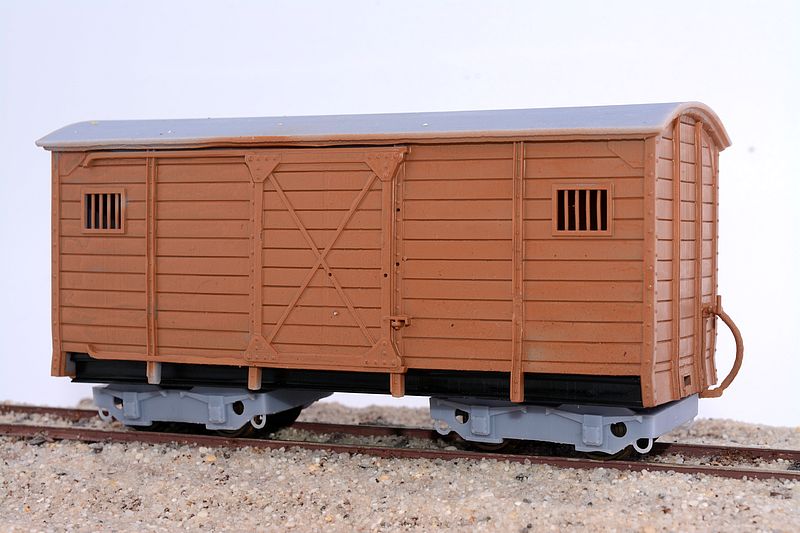
Ich muss nach dem durchtrocknen noch eine Schicht auftrage, da die Farbe noch nicht überall gedeckt hat. Ich habe die Teile zur Vorbereitung noch einmal in die Wash & Cure gepackt. Das kräftige Spülen in Alkohol hat alle Rückstände entfernt. Ab dann werden die Teile nur noch mit Einmal- Handschuhen angefasst, bis die Versiegelung drauf ist.
Für die Dächer will ich Naßschleifpapier mit feiner Körnung verwenden. Ein Dach wird mit Teerpappe- Streifen belegt, wie man es vor allem bei schon länger in Betrieb befindlichen Wagen finden kann. Das Dach wird dann nicht weiter lackiert. Das andere Dach will ich auch mit Schleifpapier beplanken, aber in einem glatt aufgeklebten Stück. Sofern möglich (muss ich erst mal testen) will ich dieses Papier aber grau lackieren, ähnlich der Farbe des verwendeten Harzes. So sollten sich doch ziemlich unterschiedliche Dächer nachbilden lassen.
Inzwischen habe ich die Wände ein zweites Mal lackiert und die Dächer mit Schleifpapier beplankt.
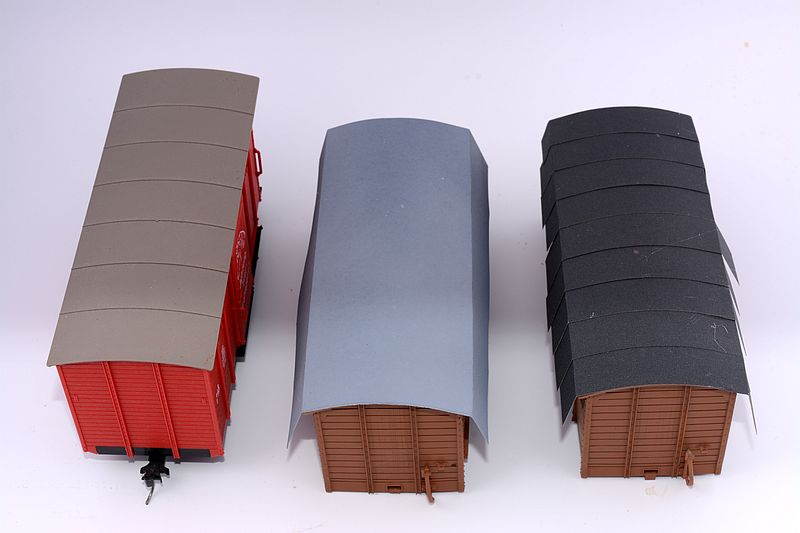
Von Links nach Rechts Magic Train G-Wagen mit unbehandeltem Dach, HF Wagen mit glatt beplanktem, grau lackiertem Schleifpapier und HF Wagen mit in Streifen geschnittenem und überlappend aufgeklebtem Schleifpapier, beides 400er Körnung. Aktuell bindet der Alleskleber noch ab. Deswegen sind die Überstände noch nicht beschnitten. Außerdem brauche ich auch noch ein paar Griffstangen, um die Wagen zu komplettieren. Und natürlich passende Drehgestelle, die ich ja leider aktuell nicht drucken kann…
Mir gefällt das in Streifen geschnittene Papier eigentlich am besten auch wenn das beim Vorbild wohl eher nicht so oft vorgekommen ist.
Nach der langen, technisch bedingten Druck- Pause habe ich heute die mit NEM Schacht versehenen Drehgestelle drucken können.
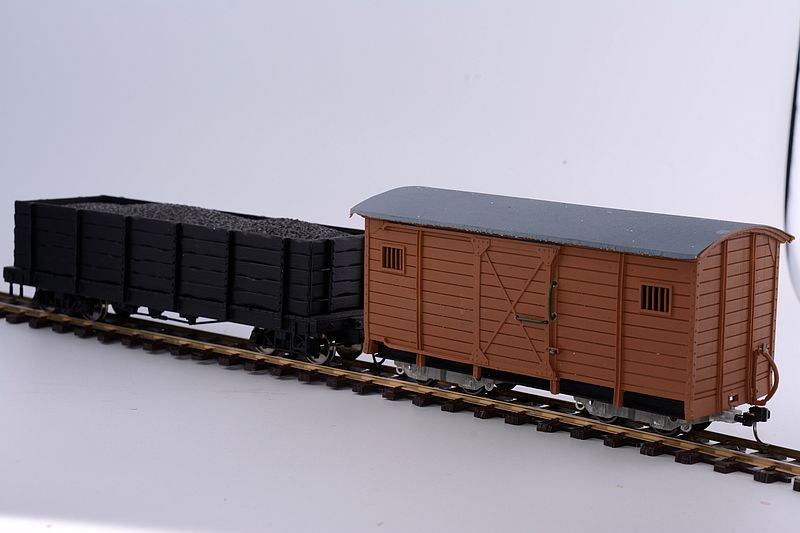
Es passt, … fast. Die Drehgestelle sind minimal zu klein geworden. Ich habe für die Ausführung mit NEM Schacht andere Ausgangsdateien verwendet. Denn es waren beim Original vier verschiedene Drehgestelle dabei. Je zwei mit und zwei ohne Bremsen- Nachbildung. Je zwei unterscheiden sich durch eine längs oder quer angeordnete “Wippe” auf den Drehkränzen. Ein Drehgestell kann also quer und eines längs kippen. So hat man eine wunderbare Dreipunktlagerung.
Bei einem Wagen mit Bremserbühne oder zumindest Bremsschläuchen schadet es sicher nichts, wenn auch Bremsen an den Drehgestellen vorhanden sind. Die Modifikationen zur Spitzenlagerung der Radsätze habe ich von den ungebremsten Drehgestellen 1 zu 1 übernommen. Dennoch sind die neu gedruckten Drehgestelle scheinbar minimal kleiner geworden. Die Radsätze kann man zwar einbauen, aber sie sitzen doch etwas stramm und laufen deswegen nicht so leicht, wie die anderen Drehgestelle. Das will ich bei der nächsten Auflage noch verbessern.
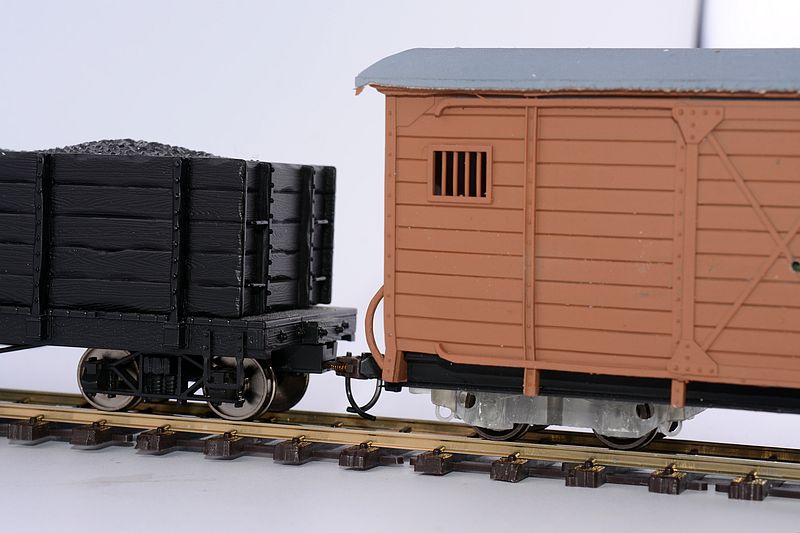
Die Höhe der Kupplung passt aber perfekt. Hier im Vergleich mit einem Großserien- Modell von Bachmann… Wenn die Kadee Kupplung passt, passen auch alle anderen NEM Kupplungen genau. Ich muss allerdings noch mal die Ecke der “Dachpappe” etwas trimmen. Da hängt noch ein Rest dran, der da nicht hin gehört.
Die RP-25 Radsätze von Tomschke (modellbahnradsatz.de) in den Maßen, 24,75mm Achsen, 11 mm Räder sind passend für die meisten Güterwagen von Roco, also sehr verbreitet. Man kann sich natürlich auch wo anders passende Radsätze holen. ich habe aber bisher immer sehr gute Erfahrungen dort gemacht. Außerdem stimmt die Qualität und der Preis. Und auch zu den HF Wagen passen die Räder nahezu perfekt. Wenn man es ganz genau haben wollen würde, müssten sie 11,1 mm Durchmesser haben. Der eine Zehntel ist aber unwichtig und wird obendrein durch die , trotz RP-25 ja immer noch zu großen, Spurkränze optisch mehr als wett gemacht.
Ich werde die Drehgestelle noch mal um 1 bis 2 Zehntel breiter machen. Dann sollten die Radsätze genau passen. Dann nur noch die Drehgestelle schwarz anmalen, die Kupplungen und Radsätze umbauen und die Drehgestelle anschrauben. Schon ist der erste HF Wagen einsatzbereit. Zumindest so lange ich noch keine Idee habe, wie ich meine Güterwagen beschrifte. ..
Der erste HF Wagen ist jetzt so weit fertig. Nun laufen die Drehgestelle auch wieder so leicht, wie ich das gewohnt bin.
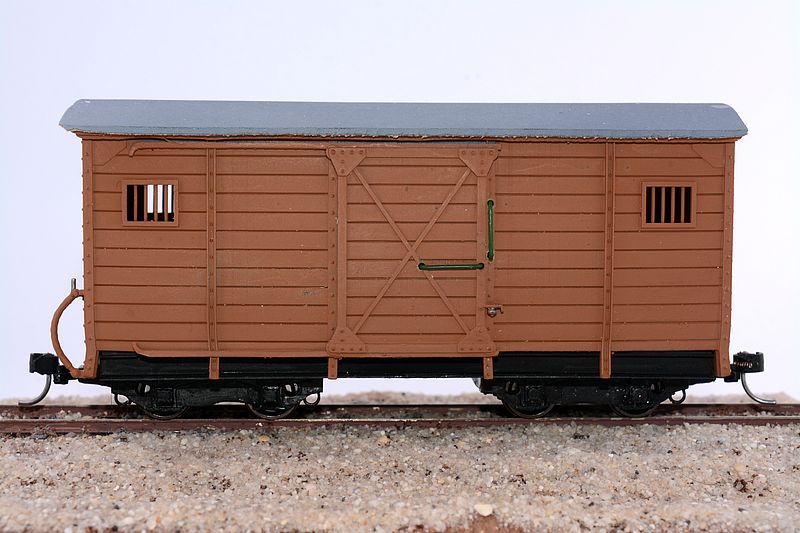
Alles in allem ein ziemlich stimmiger Wagen, finde ich. Wenn man bedenkt, das die Ausgangsdateien, die ich entsprechend modifiziert habe, ursprünglich für H0e gedacht waren, kann sich mein MD-419 durchaus auch in 0e sehen lassen, denke ich.
Die anderen Wagen müssen jetzt auch “nur” noch gedruckt werden. Die Drehgestelle sind ja dieselben, Und die sind nun genau, wie sie sein sollten. Die Modifikation der Ausgangsdateien ist inzwischen längst erledigt, also kann ich in den nächsten paar Tagen auch je einen Prototypen des MD-754 und MD-435 aufbauen.
Meine Exemplare vom MD-754 und MD-435 sind beim Lackieren. Es gibt noch viele weitere Wagen im Fundus von Uwe Stehr, mit denen man sich beschäftigen kann.
Da wären weitere HF Wagen, der MD-734 und der MD-736. Der MD-734 ist wie der MD-735, aber ohne Bremserbühne. Davon druckt aktuell ein erstes Exemplar. Der MD-736 ist noch mehr wie der MD-735, also ein Niederbordwagen mit Bühne. Nur existiert an der Bühne des MD-736 kein Geländer und auch kein Bremshebel. In sofern dürfte es such nicht um eine Bremserbühne handeln bzw. die Handbremse des MD-736 wurde irgendwann mal zurück gebaut. Dein MD-736 gibt es auch ohne Seitenwände als Flachwagen, nur mit den Stirnwänden. Auch die Typen laufen alle auf denselben Drehgestellen. In sofern werde ich sie nach und nach alle bauen.
Aber es gibt auch ganz andere Jagsttalbahn- Wagen dort zum Download. So wie es aussieht, sind die etwas schwieriger in 0e umzusetzen. Zumindest mein “Versuchsobjekt” macht durchaus Probleme. Da ich noch gar keinen PWPost und auch noch keinen “reinen” Güterzug- Packwagen habe, ist es ein PWPost geworden.
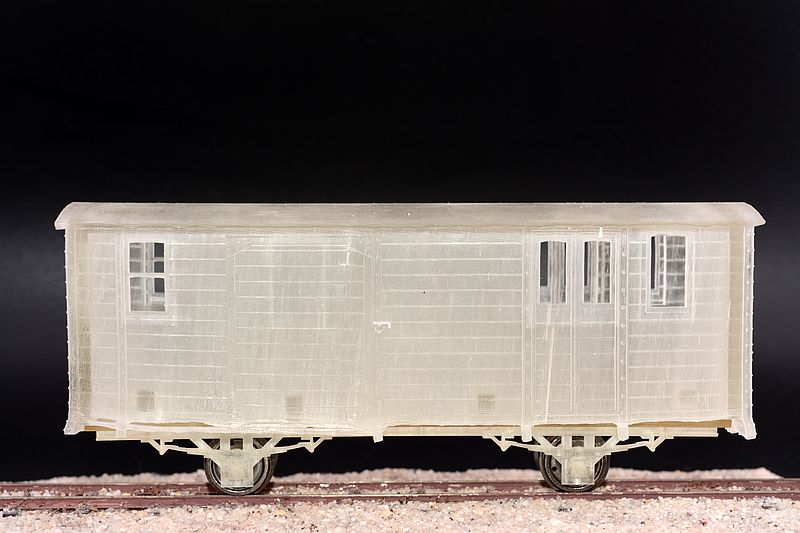
Es handelt sich um den PWPost-30. Die Datei ist ganz ohne Fahrwerk, da das H0e Modell auf einem Großserien- Fahrwerk von Liliput aufgebaut wird.
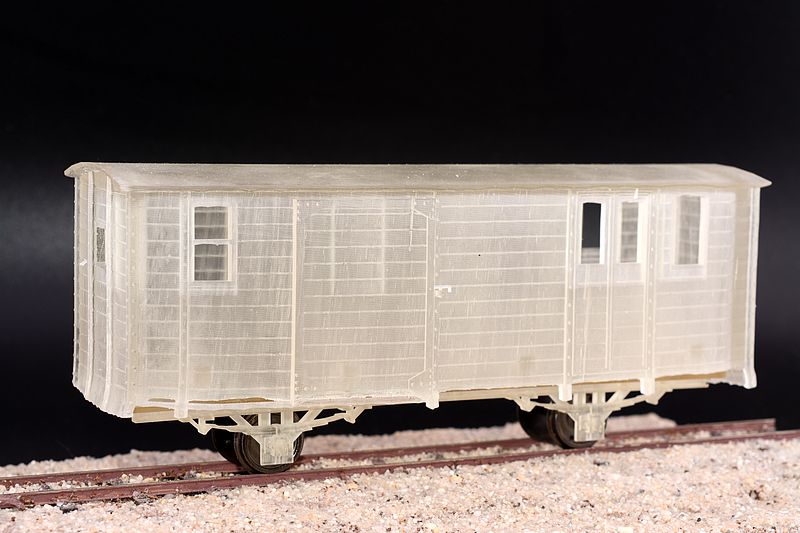
Das Dach ist massiv ausgeführt, viel zu massiv. Es ist extrem schwer, verbraucht Unmengen an Harz und zerrt obendrein zu sehr am Stützmaterial. Deswegen wird die untere Kante das Wagenkastens sehr wellig. Für den nächsten Versuch werde ich das Dach etwas aushöhlen um Harz und Gewicht zu sparen. Außerdem werde ich den Wagen wohl kopfüber drucken. So wird zwar das Dach vom Stützmaterial beschädigt, etwas, das ich sonst tunlichst vermeide. Aber wenn man dort ein “Schleifpapier- Dach” wie ich es beim MD-419 gemacht habe, vorsieht, verschwinden diese Schäden unsichtbar unter dem Schleifpapier.
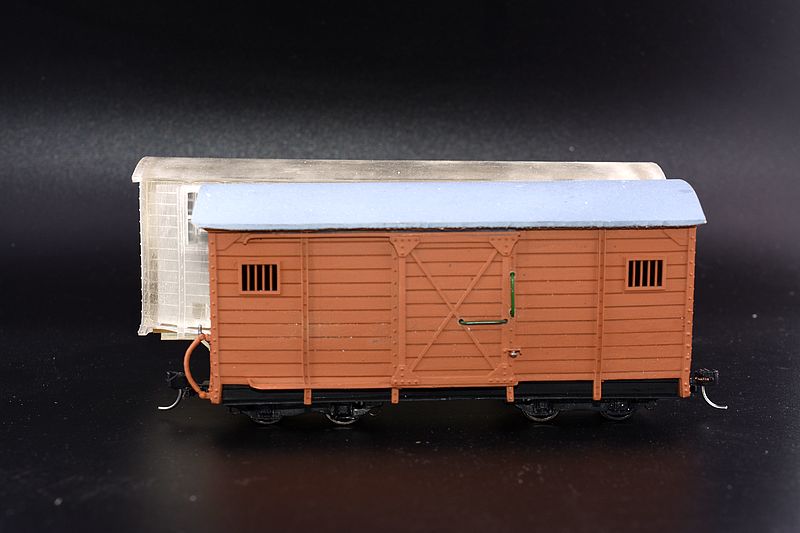
Apropos MD-419. Der PWPost-30 ist deutlich länger als der MD-419, hat im Gegensatz aber nur 2 Achsen.
Das Fahrwerk muss ich komplett selbst machen. Etwas in der passenden Länge gibt es nicht. Wenn ich die wenigen Vorbildfotos halbwegs richtig interpretiert habe, muss das Fahrwerk einen Achsstand von deutlich über 4 Meter, etwa 4,25 Meter haben. Gängige Fahrwerke haben 2,50, 2,80 Meter oder etwas in dieser Größenordnung. Das Magic Train Fahrwerk ist ebenfalls zu kurz, so das man den Wagen nicht wie beim H0e Modell auf einem Großserien- Fahrwerk aufbauen kann. H0 Fahrwerke, die es vielleicht in passender Länge geben würde, fallen aber aus, da man doch ziemlich große Räder benötigt, um ein stimmiges Gesamtbild zu bekommen. Auf den Fotos sind 14,1 mm Räder eingebaut, die sicher nicht zu groß aussehen. Dazu passen die (zu) kleinen Achslager der H0 Wagen dann überhaupt nicht mehr. Vermutlich würde man erst gar keine so großen Räder einbauen können.
Also habe ich schnell selbst was zusammen gebastelt. Fertige Achslagerblenden, die ich als Datei zur Verfügung hatte, erledigen den größten Teil der Arbeit. Dazu eine 2mm Grundplatte (um die nötige Stabilität rein zu bekommen und ein paar Rahmen- Teile. Das reicht für einen ersten Test. Die Achslager sind um ein paar Zehntel zu weit auseinander. Die Radsätze passen zwar rein und laufen sehr leicht, können aber zu leicht auch wieder raus fallen. Das ist jedes Mal dasselbe. Auf Anhieb trifft man den genau passenden Abstand sowieso nie…
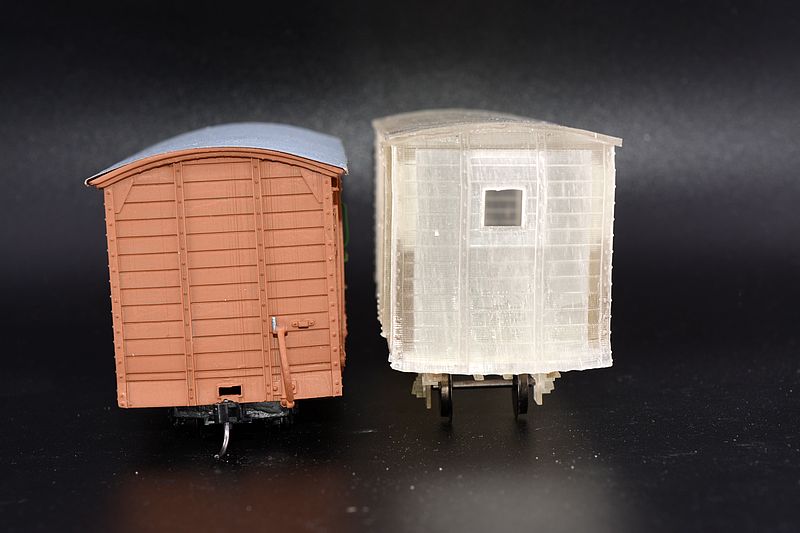
Aber wie man auf dem Foto schön sehen kann, ist der Wagen so zu hochbeinig. Tiefer versenken kann ich die Grundplatte aber nicht ohne weiteres, denn im Inneren des Wagenkastens sind Querstreben zur Versteifung eingebaut. Mal sehen, wie ich das löse. Aber so 1-2 mm muss der Aufbau noch tiefer zu liegen kommen. Das der PWPost-30 schmaler als der MD-419 ist, lässt die große Länge noch länger erscheinen. Mal sehen, wenn mir das zu lang für einen Zweiachser wird, pfriemele ich vielleicht doch ein Drehgestell- Fahrwerk darunter. Besser laufen dürfte er mit Drehgestellen auf jeden Fall. Vielleicht mache ich auch beide Varianten, mal sehen.
Am Fahrwerk fehlen noch Aufnahmen für die Kupplungen. Die kann ich ja erst nach dem Testdruck in der Höhe justieren. Das Vorbild hat ein hölzernes Trittbrett durchgehend von der Schiebetür bis zu den Flügeltüren des Post- Abteils. Das eigentliche Trittbrett wird (mal wieder) aus Kaffee- Rührstäbchen hergestellt. Aber passende Halter drucke ich lieber gleich mit. Dann sitzen sie an den richtigen Stellen. Das muss also auch noch ans Fahrwerk dran.
Ob ich mich irgendwann mal an den “langen Lulatsch”, den MD-111 wage, weiß ich noch nicht. Der Wagen würde 250mm lang werden und somit ein erkleckliches Stück länger als selbst die Bachmann Wildwest- Personenwagen, die bisher mit Abstand die längsten Wagen in meinem Bestand sind. Aber zumindest gibt es dafür ebenfalls passende Dateien. Ob ich den Wagenkasten aber überhaupt in meinem Drucker unterbringen kann, steht noch gar nicht fest.
Aus Spaß habe ich mal die STL für den MD-111 auf 1:45 skaliert und in den Slicer eingeladen. Keine Chance, das Ding ist viel zu lang für meine Hardware…
Nachdem ich netterweise den Hinweis bekam, dass das Original wohl doch deutlich weniger als 4 Meter Achsstand hat und ein Magic Train Fahrwerk passen sollte, habe ich mal einen Versuch gewagt und einen MT Wagen auseinander gebaut. Einzelne MT Fahrwerke habe ich nämlich nicht auf Vorrat.
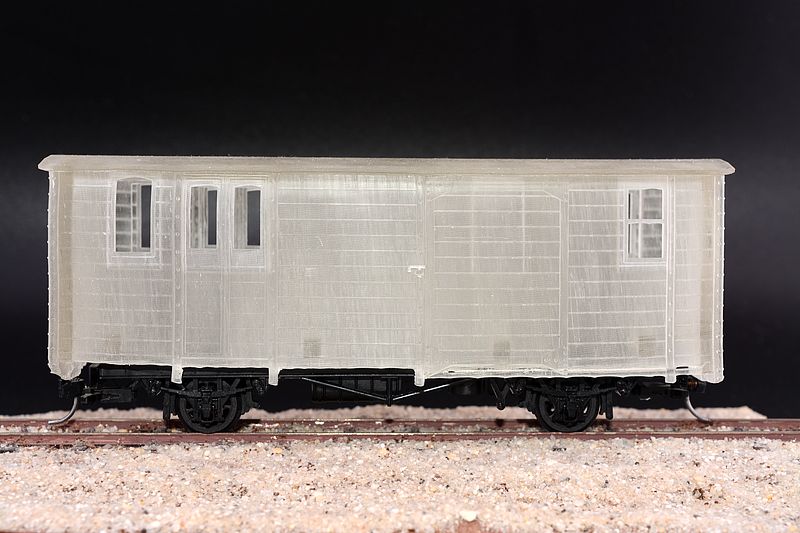
Und siehe da, es passt, und das sogar recht gut. Der Wagen liegt auch nicht mehr ganz so hoch. Man muss aber leicht am MT Fahrwerk herum schnibbeln, damit es richtig passt. An den Stirnseiten, da wo die Bühnen eingeklipst werden, ist es minimal breiter als der Ausschnitt im Wagenkasten. Ich hab den Aufbau zum Probieren halt schräg aufs Fahrwerk gelegt.
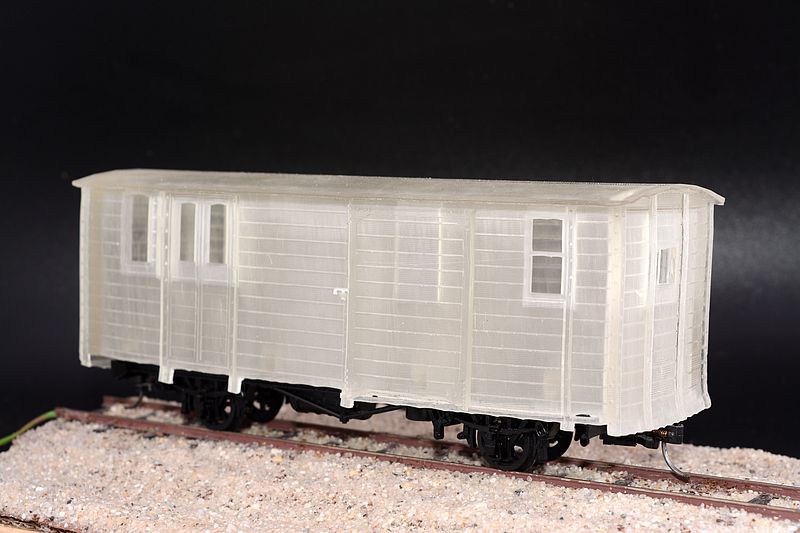
Eine zusätzliche Platte muss auch wohl rein, weil das Fahrzeug sonst von unten an vielen Stellen völlig offen ist. Ob die ganz langen Kadee NEM Kupplungen ausreichen, um unter dem doch längeren Wagenkasten hervor zu kommen, muss ich auch erst noch sehen. Auf dem Foto sind die “Medium” Kupplungen eingebaut. Sonst muss ich auch noch an den Kupplungsschächten herum basteln.
Und es stellt sich die Frage, wo bekommt man ein MT Fahrwerk her, ohne dafür erst eine Bank ausrauben zu müssen? Noch hat Roco das neue MT Startset ja nicht geliefert. Vorher treiben die Preise auf eBay schnell noch besonders seltsame Blüten. Ein Güterwagen für 75€, eine Stainz mit 3 Personenwagen für 500€, eher die Norm als die Ausnahme zur Zeit…
Generell denke ich aber, das ist gar kein so schlechter Weg. Wenn ich das Dach noch etwas leichter bekomme, sollte der Wagen dann genau wie ein “normaler” MT Wagen laufen…
Die extra langen Kadee NEM (No#20) Kupplungen reichen für den PWPost nicht aus. Also muss ich wohl eine NEM Verlängerung bauen.
Als Abschluss für heute gibt es noch die ersten Bilder vom MD-434
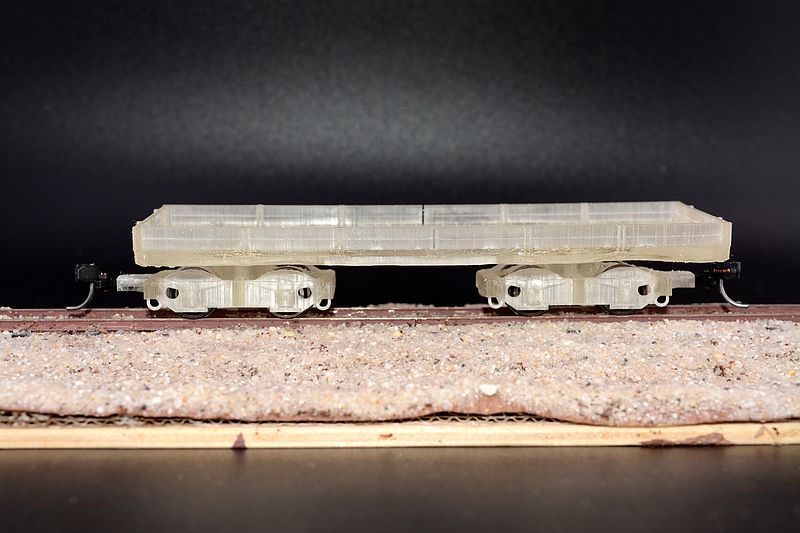
An sich ganz nett, aber die Drehgestelle sitzen wie bei einem Wagen mit Bühne, also unsymmetrisch. Ich weiß nicht, ob das so richtig ist oder eine Vereinfachung bei der Konstruktion.
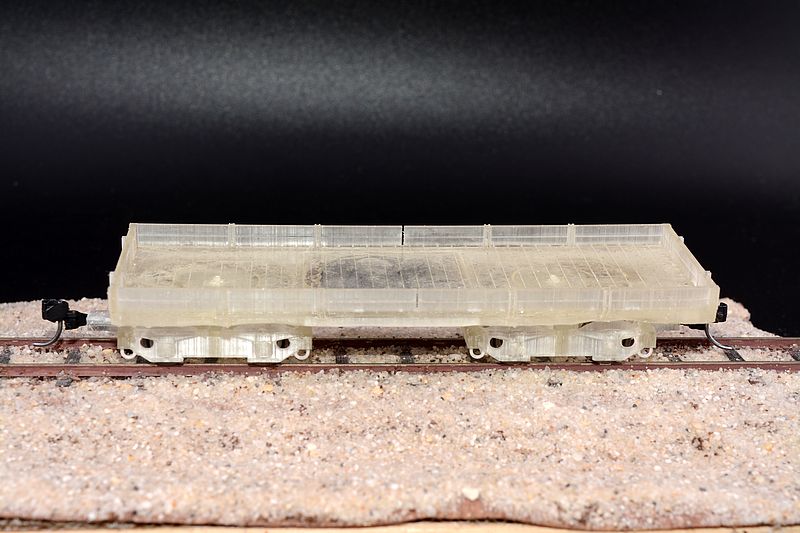
Dieses Exemplar ist aber jetzt so weit fertig und wird auch mit lackiert und eingesetzt.
Fürs erste war es das aber jetzt. Inzwischen habe ich sogar meinen Drucker, der seit Tagen rund um die Uhr läuft, an seine Grenzen getrieben. Genauer gesagt den USB Stick für die Daten. Die Daten lassen sich plötzlich nicht mehr lesen und so kann dann auch nicht gedruckt werden. Da ich die Daten natürlich noch auf meinem PC habe, ist das kein großes Drama, sollte der Stick tatsächlich hinüber sein. Auch wenn es langsam fast schon schwierig wird so kleine USB Sticks aufzutreiben, damit sie “native” mit FAT32 formatiert werden können, habe ich doch noch einige davon auf Vorrat. Ist ja ein “Pfennigartikel” heutzutage…
Ich habe mal ein neues Fahrwerk gemacht, passend zum PWPost. Es hat umgerechnet 3,80 Meter Achsstand, genau wie das Vorbild.
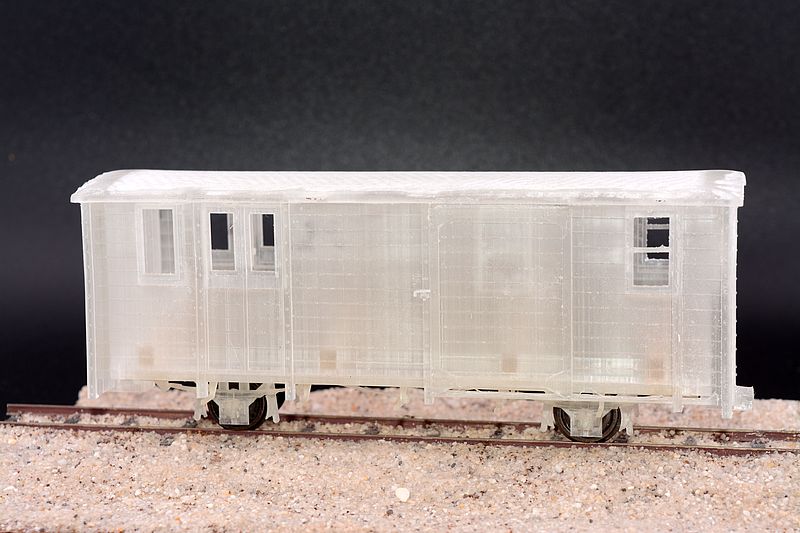
Ich habe sowohl den PWPost-30 als auch den PWPost-31 gedruckt. Ich kann aber beim besten Willen keinen Unterschied erkennen. Um welchen der beiden Wagen es sich auf dem Foto handelt, weiß ich nicht.
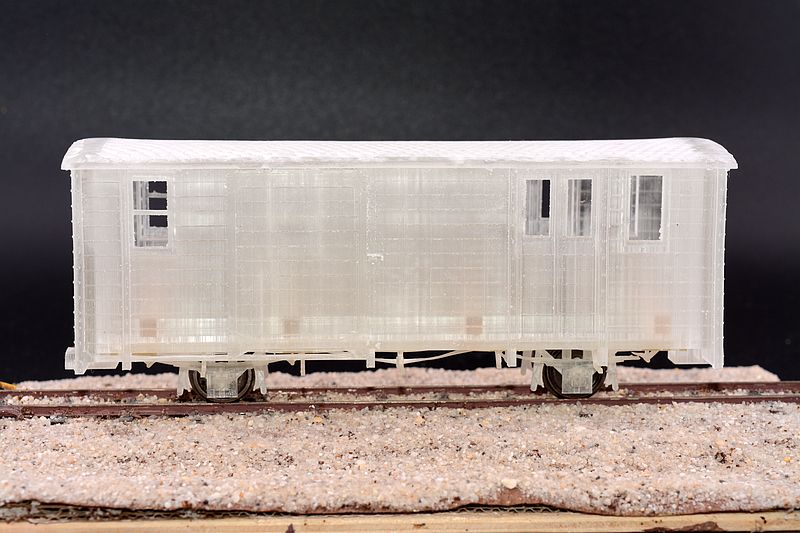
So werde ich die beiden Wagen dann fertig stellen. Die Drucke haben ein ausgehöhltes Dach und wurden “kopfüber” gedruckt. So habe ich den Harzverbrauch glatt halbieren können.
Aber die Wagen sind auf jeden Fall für Zweiachser sehr, sehr lang. Mal sehen, ob sie vernünftig fahren. Sehr leicht laufen tun sie auf jeden Fall. Die schon mehrfach bewährte Spitzenlagerung leistet auch hier gute Arbeit.
Ich muss mir angewöhnen häufiger auch die fertigen Fahrzeuge zu zeigen. Das möchte ich hiermit nachholen.
Zunächst noch zum PWPost. Meine Eigenbau- Fahrwerke sitzen etwas zu tief im Wagenkasten drin. Dasselbe würde übrigens auch mit einem MT Fahrwerk passieren.
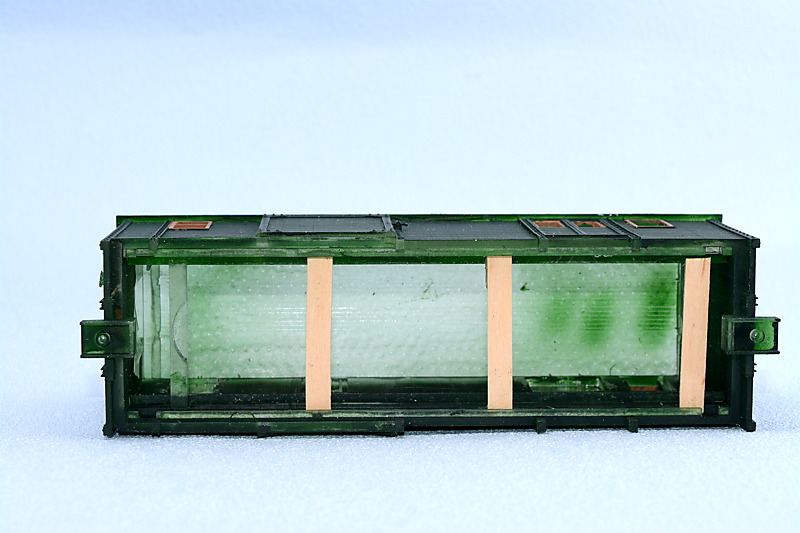
Zum Glück gibt es Kaffee- Rührstäbchen, die Allzweckwaffe des Modellbauers. Im Inneren des Aufbaus gibt es 4 Stege, auf denen das Fahrwerk zu liegen kommt. Klebt man dort Abschnitte von Rührstäbchen drauf, passt die Höhe wieder.
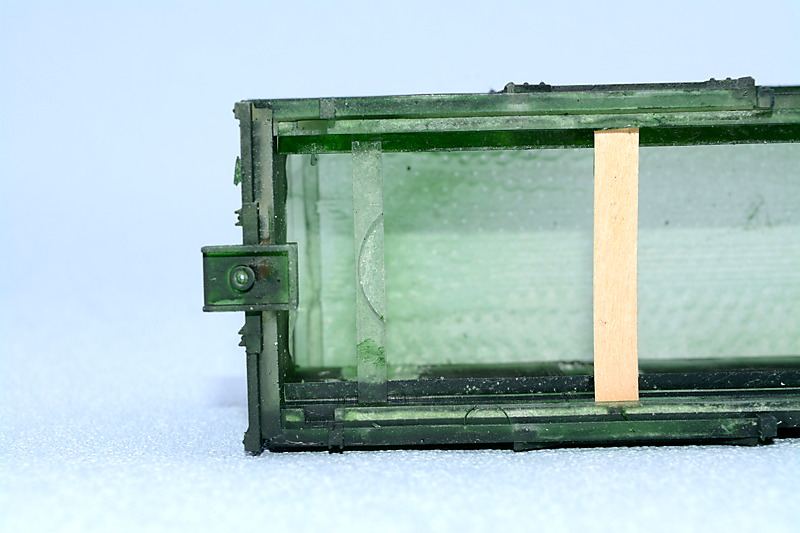
Im Original ist der Aufbau ja für ein Liliput H0e Fahrwerk vorgesehen. Die Original- Datensätze sind eben für H0e und nicht für 0e gedacht. Dafür das die Dateien (fast) auf doppelte Größe skaliert werden mussten, sind die Materialstärken und Details wirklich sehr gut. Deswegen habe ich ja schon diverse Wagen aus diesen Datensätzen gebaut.
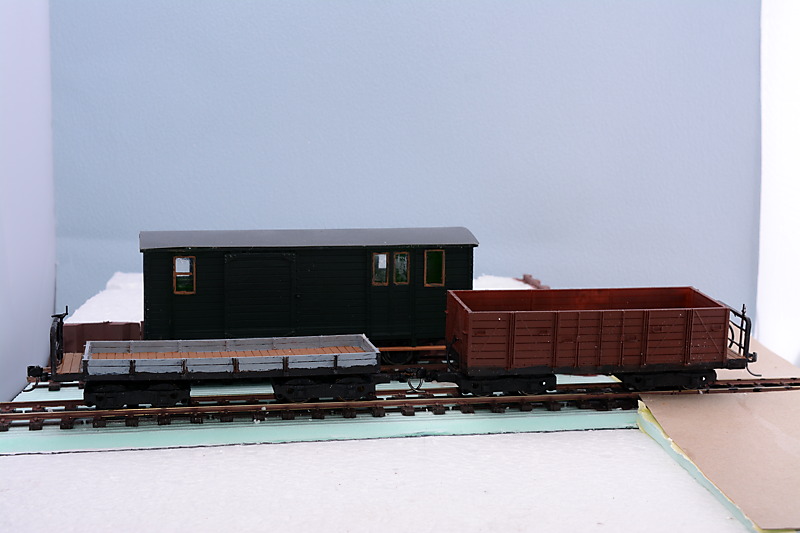
Hier haben wir gleich drei Modelle auf einmal. Hinten der PWPost, davor ein MD754 und ein MD435. Leider ist mir die Lackierung beim MD435 misslungen. Das kann so nicht bleiben. Was genau ich mache, weiß ich noch nicht. Mal sehen.
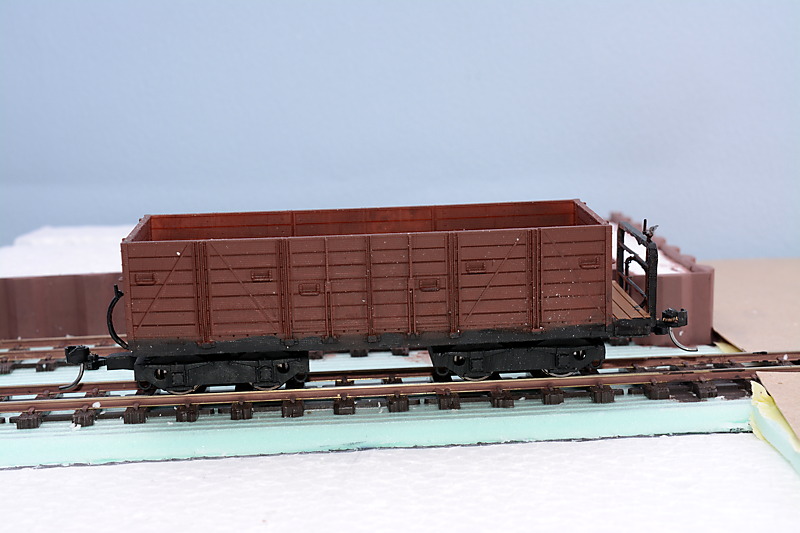
Beim MD 754 musste ich das Geländer an der Bremserbühne erhöhen. Es reicht ja original nicht man bis an die Knie eines 1:50 “Chinesen”. So passt das jetzt aber ganz gut.
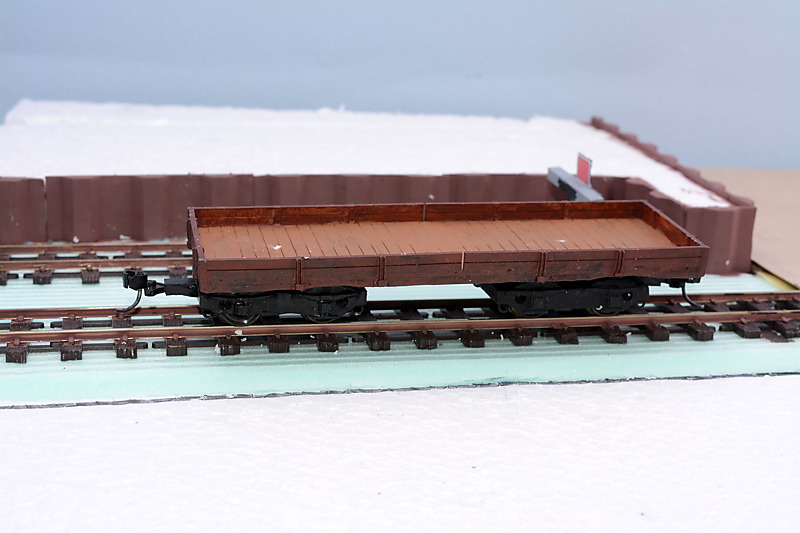
Auch einen MD436 habe ich inzwischen fertig gebaut. Den MD 436 gibt es auch mit demontierten Seitenwänden. Diese Variante habe ich bisher aber noch nicht gemacht. Ich muss demnächst auch erst wieder Radsätze und Kupplungen organisieren. Beides wird knapp… Bevor ich hier weiter mache (es gibt noch unzählige weitere Datensätze auf der Seite von Herrn Stehr), will ich aber erst mal die anderen Baustellen zumindest ein wenig abarbeiten.
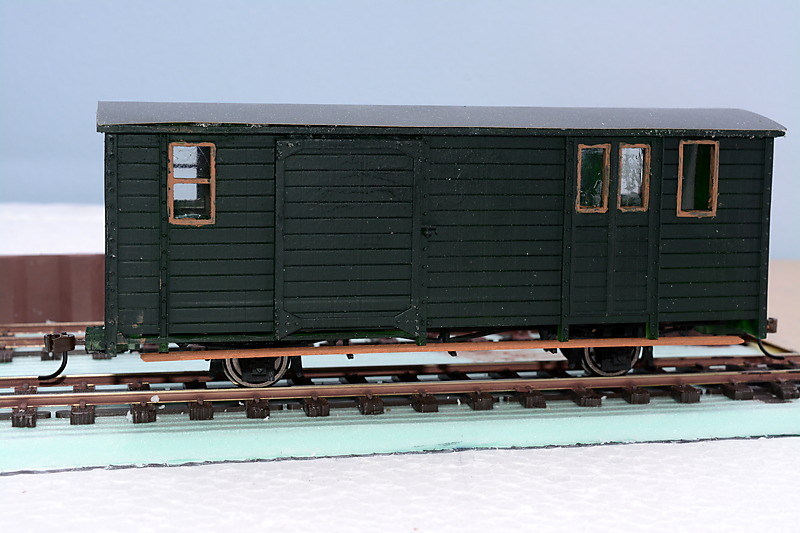
Und zum Abschluss ein Foto vom PWPost. Die Trittbretter sind, welch Wunder, Kaffee- Rührstäbchen. Die RP25 Radsätze sind von Hornby und haben 14,1mm Durchmesser. An die Verglasung kommt man nur extrem schlecht heran. Ich dachte, wenn ich sie mit Micro Crystal Clear einklebe, verschmieren die Scheiben nicht so. Leider ist das doch der Fall. Ich hätte besser gar keine Verglasung eingebaut. Vielleicht drücke ich sie einfach wieder raus.
Auf vielfachen Wunsch eines einzelnen Herren habe ich eine neue Variante der HF Wagen “kreiert”. Mein Kumpel Manfred wollte gerne einen HF G Wagen mit Bremserbühne haben. Bei den zahlreichen Dateien von Uwe Stehr ist aber kein solcher Wagen dabei.
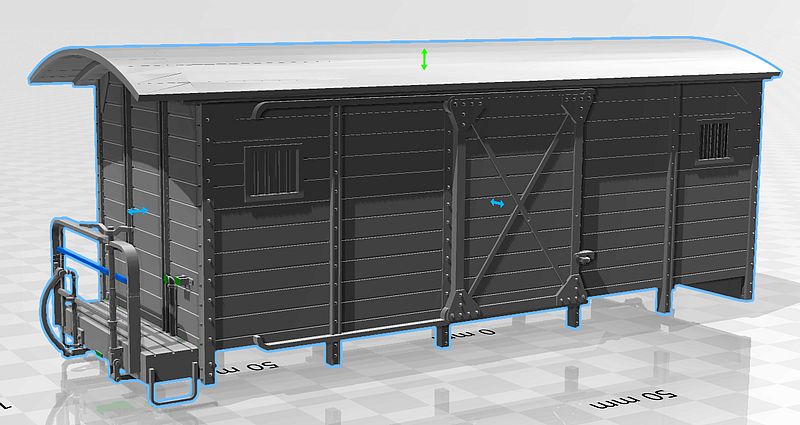
Also habe ich ein wenig in der CAD gespielt und aus dem Aufbau und Fahrwerk des MD 419 sowie der Bühne des MD-754 so einen Wagen zusammengeklöppelt.
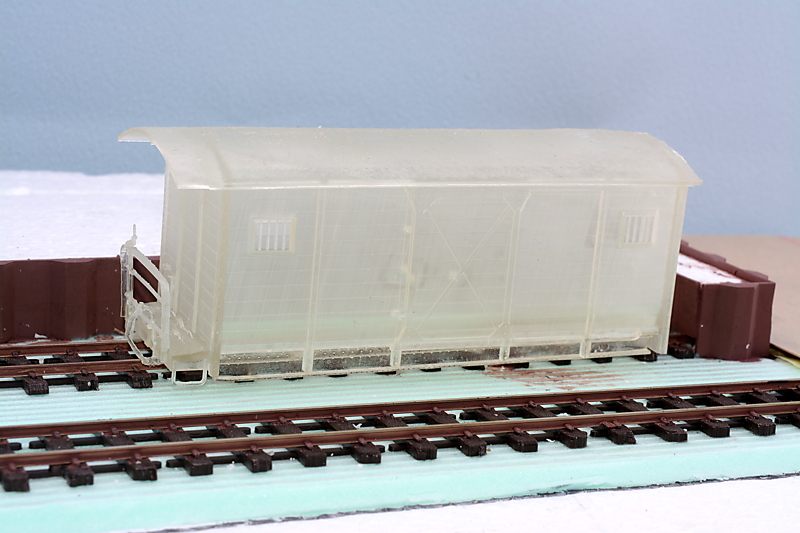
Ein erster Probedruck. Sieht doch fast wie gewollt aus, oder? Ein paar Kompromisse musste ich eingehen. So ließ sich der Bremsschlauch nicht völlig beseitigen. Auch das in die Länge ziehen des Dachs ist als solches zu erkennen, wenn man genau hin schaut.
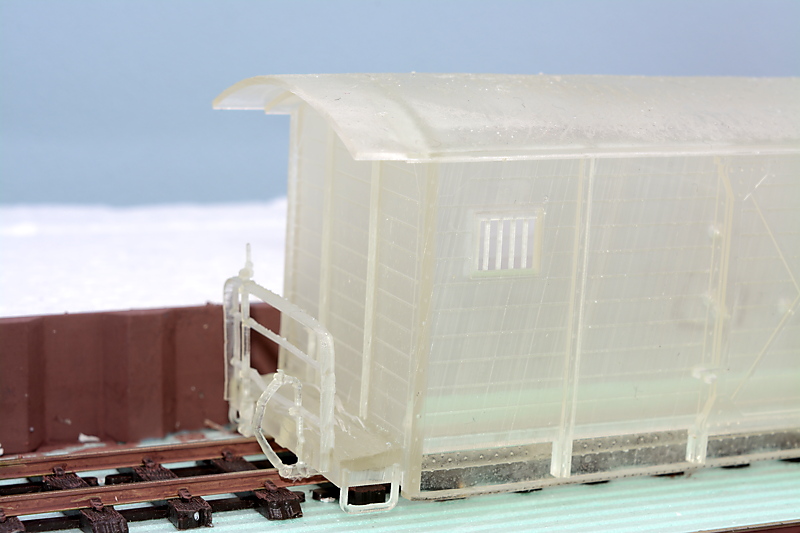
Aber im Prinzip geht es so durchaus. Das Probe- Exemplar werde ich auf jeden Fall fertig bauen, denn auch ich mag Wagen mit Bremserbühne.
Der selbe Herr hatte noch einen “Spezialauftrag” für mich. Er wollte gerne NEM Schächte haben, solche, wie ich sie an diversen meiner Fahrzeuge angebaut habe.
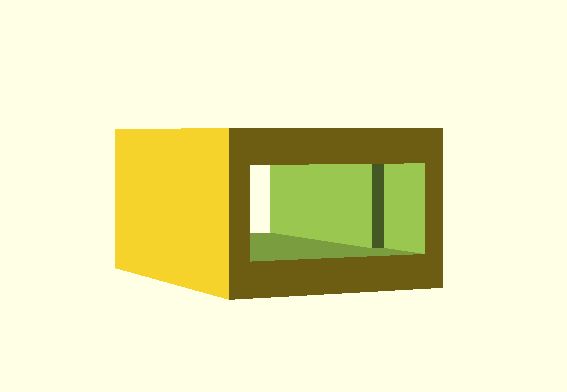
Ein einfaches Vierkantrohr funktioniert nicht, da man für die Kupplung eine Kante zum einhaken benötigt. Kann man oben schön erkennen.
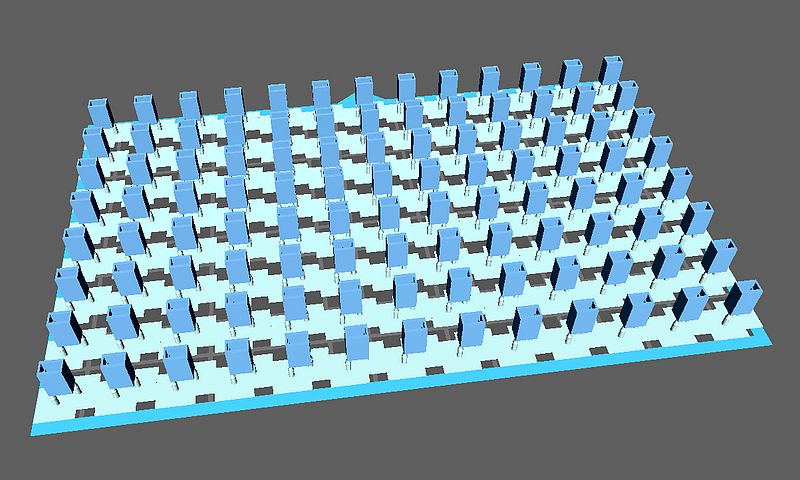
104 Schachte passen auf einmal in meinen Drucker, ohne sich zu drängeln.
Nach dem Drucken waren alle Schächte schön ordentlich vorhanden. Doch nach dem Waschen sah es plötzlich so aus:
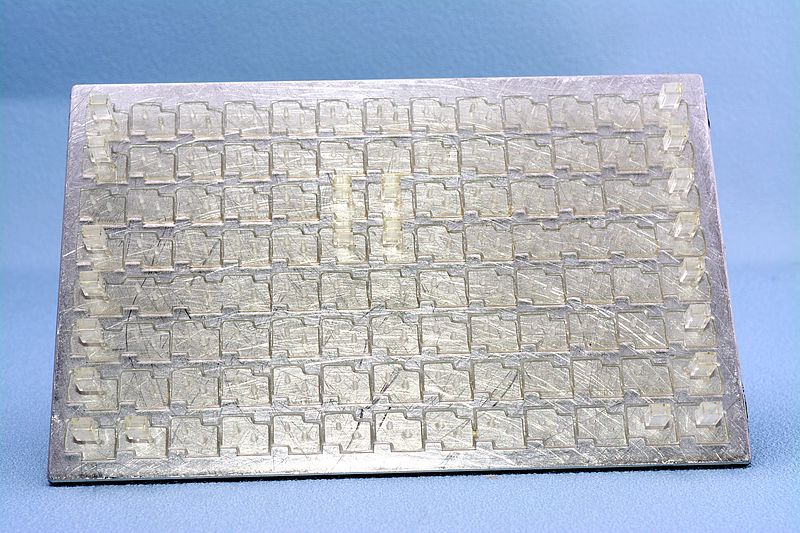
Die meisten Schächte sind ausgebüxt und schwimmen irgendwo in der Waschflüssigkeit herum.. Da hat die Wash&Cure wohl zu viel Strömung erzeugt. Also musste ich das ganze durchsieben, um die Schächte wieder einzufangen.
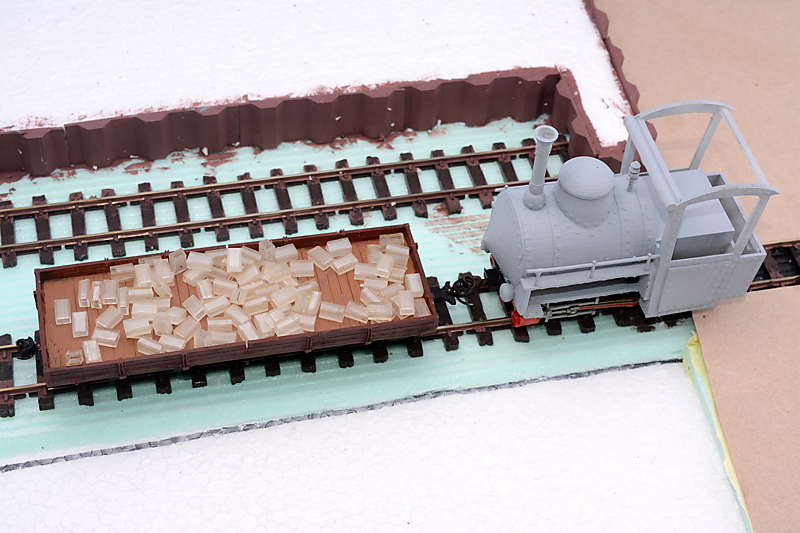
Ich habe nicht nachgezählt, aber die meisten Schächte sollten sich wieder eingefunden haben.