Hier nun der letzte Teil des Bauberichts von meiner Mini- CNC Fräse. Nachdem der Aufbau fertig gestellt wurde, musste zunächst mal die passende Software- Ausstattung gefunden werden. Und das hat sich als extrem schwierig herausgestellt.
Es ist zwar überhaupt kein Problem, anständige CAD Software zum Nulltarif zu bekommen (LibreCAD, FreeCAD, Inkscape, QCAD,…) . Die Konstruktion der Fräsobjekte lässt sich also ganz leicht mit Open Source oder Freeware erledigen.
Aber die CAM Software, die aus den in der CAD Software erstellten Zeichnungen G-Code für die Fräse erzeugt, das ist ein großes Problem. Alles, was brauchbar ist, kostet ein Vermögen. Ich sehe nicht ein, zu einer 200€ Fräse eine 2000€ Software wie Solidworks dazu zu kaufen. Mal ganz abgesehen davon, das ich mir das sowieso nie leisten könnte. Es gibt einige “Free” Programme, das sind aber alles nur Demos, mit teilweise extremen Einschränkungen. So legt beispielsweise EstlCam nach dreimaliger Benutzung bei jedem Mausklick geschlagene 180 Sekunden (wirklich, 3 Minuten) Pause ein, in der ein Nerf- Requester gezeigt wird, in dem man aufgefordert wird, die Urlaubskasse der Autoren zu füllen. Da man diesen Requester nicht wegklicken oder auch nur in den Hintergrund schieben kann, ist der Recher dann vollständig blockiert. Obendrein ist der von EstlCam erzeugte G-Code voller Fehler. Damit steht natürlich fest, das ich die Urlaubskasse der Autoren definitiv nicht auffüllen werde. Auch andere als “free” beworbene CAM Programme sind immer nur stark eingeschränkte Demos, mit denen man nicht wirklich etwas anfangen kann.
Bei der Fräse selbst ist auch kein CAM Programm mit dabei. Nur das (tadellos funktionierende) Steuerprogramm “GRBL Control” wird mitgeliefert…
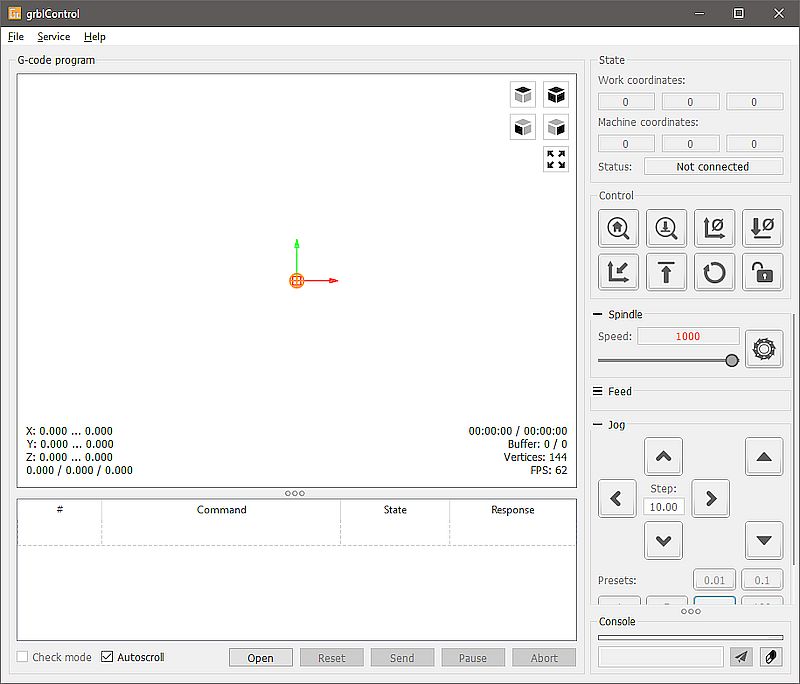
Daneben existiert ein (ursprünglich für Linux gedachtes) Python Programm namens bCNC. Das Programm kombiniert CAD und CAM Software in einem Open Source Projekt. Allerdings benötigt es eine uralte Python Version und diverse Zusatz- Pakete, ganz Linux typisch, um ein Programm zu nutzen, muss man erst mal hunderte von “Dependencies” installieren. Trotzdem ist der Erfolg fraglich. Genau so hier. Ich bin wirklich kein Computer Anfänger, aber mir ist es nicht gelungen, das Programm ans laufen zu bekommen…
Es gibt ein Plugin für Inkscape das aus der in Inkscape erstellen Zeichnung G-Code erzeugt. Das ist aber inoffiziell, der Support dafür auf Russisch und obendrein extrem kompliziert zu bedienen.
Für das die “Professional” Version der OpenSource Software QCAD gibt es ein CAM Modul. Das kostet aber auch schon dreistellige Beträge, erscheint mir aber fast noch das beste Preis- Leistungsverhältnis zu haben. Dachte ich zumindest…
Als ich schon verzweifelt aufgeben wollte, bin ich doch noch fündig geworden. Der US- Hersteller Carbide, der halbwegs preisgünstige (1500$ bis 2500$) CNC Fräsen, die ähnlich wie meine China Fräse auch auf der Open Source Firmware GRBL basieren, herstellt, hat sein hauseigenes CAD/CAM Programm, das bisher nur für die eigenen Kunden verfügbar war, seit kurzem für jeden freigegeben. Das Programm heißt “Carbide Create” und ist, nachdem man sich für eine Mailing Liste angemeldet hat, kostenlos zu nutzen. Für sowas gibt es ja gottseidank Wegwerf- Email Adressen. Außerdem funktioniert das Abmelden von dem Newsletter tatsächlich.
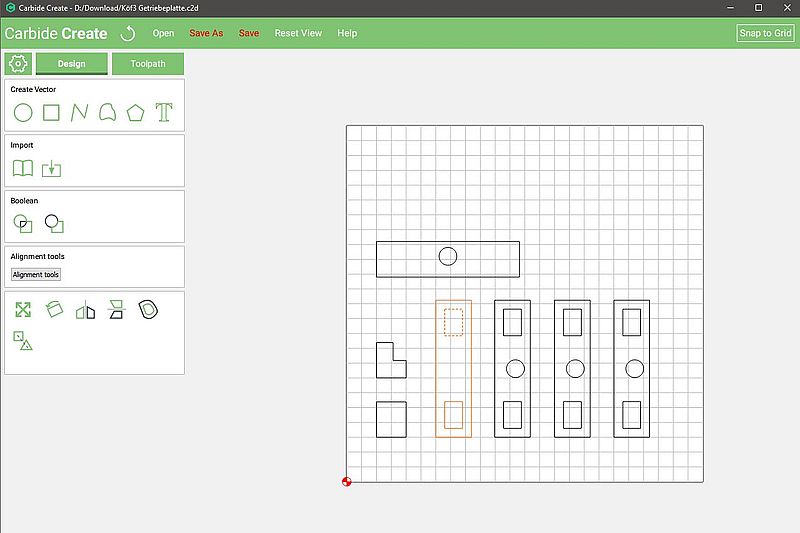
Carbide Create kann SVG und DXF Dateien importieren und stellt darüber hinaus umfangreiche Tools zum Konstruieren von Fräs- Objekten bereit. Man hat Grundformen, die man verändern und kombinieren kann, genau so wie Text oder Bool- Operationen. Vor allem ist es wunderbar einfach möglich, die Abmessungen und Anordnungen ganz präzise einzustellen. Eine Bitmap (jpg, bmp oder so was) lässt sich halb- transparent in den Hintergrund legen und nachzeichnen. Wenn man also eine Zeichnung einer Lok aus dem Internet herunter geladen oder eingescannt hat, kann man diese passend skaliert als Hintergrund nutzen und so die Formen präzise nachzeichnen.
Wenn die Zeichnung steht (egal ob importiert oder in Carbide Create erzeugt) generiert mal die Pfade für die Maschine (“Toolpath” auf Englisch). Das ist dann jetzt das wichtige “CAM” Modul. Hierfür stehen diverse Werkzeuge zur Verfügung. Man kann Innen- oder Außen fräsen, “pockets” also Vertiefungen, die nicht komplett durch getrennt werden sondern beliebig tief in das Material eingraviert werden, erzeugen lassen. Auch die “tabs” also die Haltestege, damit das gefräste Teil noch am äußeren Material hängt, lassen sich ganz einfach erzeugen, positionieren und anpassen. Man kann das Ergebnis simulieren lassen. Dann wird eine 3D Ansicht des Projekts erstellt, so wie es nachher tatsächlich gefräst wird. Passt alles, lässt sich das Projekt als G-Code speichern und mit einer beliebigen Fräse, also auch meiner CNC 3018 verarbeiten…
Für einen Einsteiger wie mich, der erst noch alles lernen muss, ist Carbide Create wirklich gut geeignet. Dazu gibt es viele Video- Tutorials, so das der Einstieg leicht gemacht wird. Zwar ist das alles nur auf Englisch zu bekommen, dafür aber wirklich kostenlos und ohne Einschränkungen. Ein Grund mehr, endlich Englisch zu lernen…
Carbide Create ist das einzige CAD/CAM Programm, das ich finden konnte welches voll funktionsfähig, einfach zu bedienen und trotzdem kostenlos verfügbar ist. Deswegen bekommt es meine uneingeschränkte Empfehlung. Carbide Create gibt es für Windows und Mac, nicht aber für Linux.
Jetzt, da die Software Frage zumindest vorerst geklärt ist stehen nur noch die letzten Tuning- Maßnahmen an, um dann eine wirklich einsatzfähige CNC Fräse zu haben. Ich benötige noch eine anständige Aufnahme für die Fräser. Die mitgelieferte Messinghülse ist alles, nur nicht präzise. Damit kann man keinen Rundlauf hin bekommen. Also muss eine neue Aufnahme her. Es bietet sich an, den weit verbreiteten und oft bei dieser Art Fräsen verwendeten Standard ER11 zu verwenden. Im direkten Vergleich zwischen der ER11 Spannzangen- Aufnahme und der mitgelieferten Messinghülse ahnt man schon, das jetzt alles besser wird.
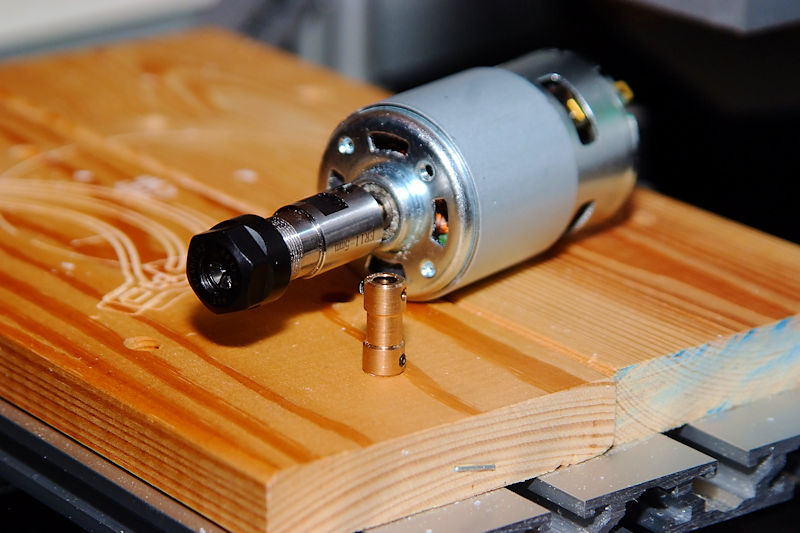
Um die Halterung zu montieren, musste ich sie mit dem Lötkolben erhitzen. Die Bohrung ist wirklich stramm sitzend. Die Madenschrauben sind eigentlich nicht nötig, so stramm wie die Halterung auf die Welle gepresst ist. Das ist natürlich beabsichtigt, damit der Fräser sauber rund läuft. In der Tat ist der Rundlauf mit bloßem Auge deutlich erkennbar besser als mit der Messinghülse.
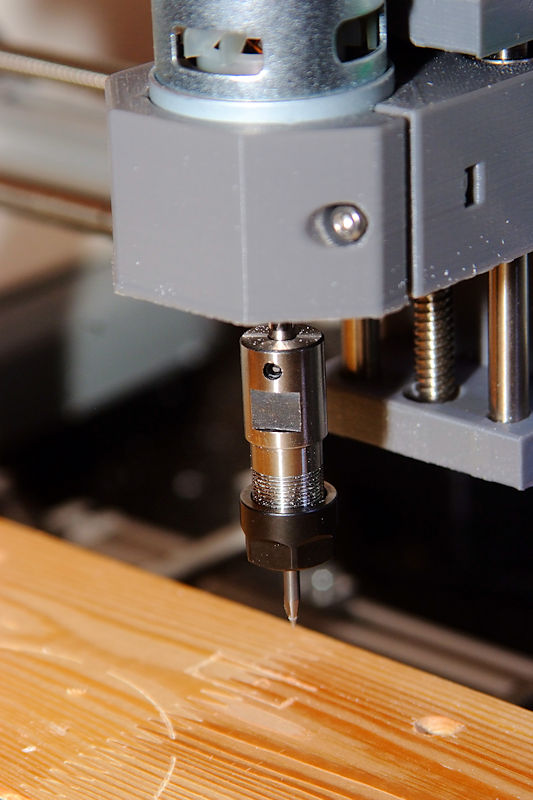
Jetzt fehlen mir nur noch anständige Fräser. Dabei kann man wirklich viel Geld loswerden. Aber ein Fräser, der genau so viel kostet wie meine ganze Fräse, das wäre dann doch wohl des Guten zu viel… Erst mal musste ich raus finden, welche Fräser für Polystyrol geeignet sind. Ein erster Versuch mit den Fräsern aus einem Gravurset mit Mini- Bohrmaschine endete katastrophal. Das Polystyrol ist nur am Fräser fest geschmolzen, aber nicht geschnitten worden.
Ich habe mich nach längerer Recherche für einen Einschneidenfräser entschieden. Bestellt habe ich die Fräser bei cnc-plus. Dort gab es passende und qualitativ relativ gute Fräser für ca 5€ das Stück. Mal sehen, wann sie ankommen.
Außerdem habe ich in China eine Satz Spannzangen mit Durchmessern von 1 bis 7 mm bestellt. Die sollten so Ende November Anfang Dezember ankommen. Dann kann man neben den Standard 3,2 mm Fräsern auch mal kleinere oder größere Bohrer verwenden. Als Standbohrmaschine lässt sich die Fräse nämlich auch “zweckentfremden”…
Wer also auch so eine Fräse bauen will, sollte entweder gleich einen Bausatz mit ER11 Spannzangenaufnahme bestellen oder zumindest die ca 15€ für so ein Teil mit einkalkulieren. Ohne das wird man sicher nicht glücklich mit der Fräse…
Außerdem habe ich im Internet nach dem Laser- Modul für meine Fräse recherchiert. Im Prinzip gibt es ja 3 verschiedene Laser- Module. Eines mit einem 500 mW Laser, eines mit einem 2.5 Watt Laser und eines mit einem 5,5 Watt Laser. Das “Kleine” ist nur Spielzeug, damit kann man gravieren, aber nicht wirklich schneiden. Das “Große” ist schon sehr kräftig, aber im Verhältnis sehr teuer und aktuell so gut wie nicht aufzutreiben. Das “mittlere” Modul hingegen ist sehr preisgünstig so um ca 50€ herum zu bekommen. Und es ist kraftvoll genug um MDF, Sperrholz und sogar Acryl (kein Transparentes oder Blaues, aber Rotes oder Schwarzes z.B.) bis ca 5 mm problemlos zu schneiden. Dünne Sachen wie Karton stellen natürlich überhaupt kein Problem dar. Ich denke, das 2,5 Watt Laser Modul stellt wirklich eine sinnvolle Ergänzung dar. Damit kann man dann Holz oder Karton verarbeiten und zwar bestimmt besser als mit dem Fräser. Das 2.5 Watt Modul hat es damit auf meine Wunschliste für 2019 ziemlich weit nach oben geschafft.
Hiermit ist der Baubericht zu meiner CNC Fräse abgeschlossen. Wenn es wirklich nächstes Jahr das Laser Modul gibt, gibt es dazu einen eigenen Bericht.
Inzwischen habe ich die ersten Teile aus der Fräse, die ich tatsächlich einsetzen kann und werde. Es handelt sich um die Antriebs- Halterung für meine im Bau befindliche GEC Lok aus einem Slimrails Bausatz, für die ich eine H0 Köf 3 von Roco als Antriebsspender verwende.
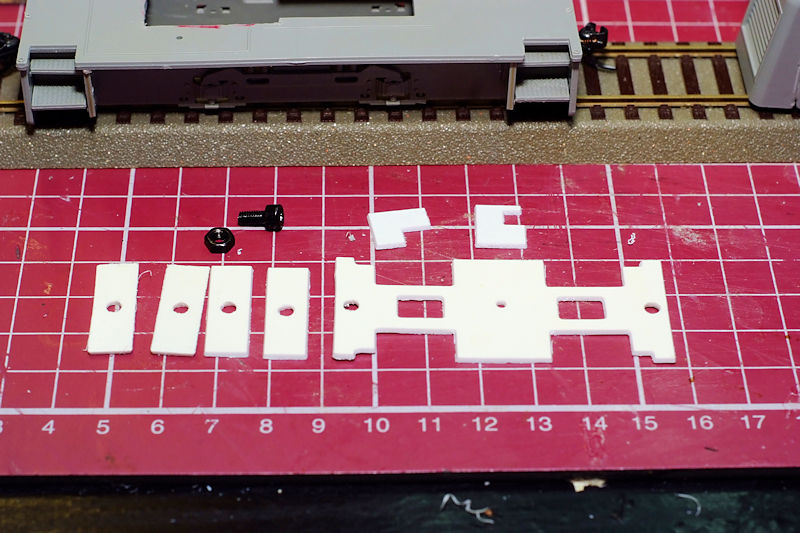
Die Präzision der Teile ist mindestens so gut wie die der Bausatz Teile aus Plastik- Spritzguss und damit mehr als ausreichend für meine Zwecke. Auf dem Foto sind die Teile noch nicht entgratet oder anders nach bearbeitet sondern exakt so, wie sie aus der Fräse kommen. Mit einem Skalpell und Lineal hätte ich das nie auch nur ansatzweise so gut hin bekommen. Das wäre in diesem Fall zwar nicht unbedingt nötig gewesen, da die Teile sowieso unsichtbar unter der Lok eingebaut werden, aber so ist es trotzdem viel besser…
Was hat der Spaß nun insgesamt gekostet und was musste ich alles machen, damit die Fräse einsatzbereit wurde?
Der Bausatz der Fräse hat bei Ebay 199€ incl Versand aus Deutschland gekostet. Die (zwingend notwendige) ER11 Spannzange hat zusammen mit dem 1/8 Zoll Einsatz für die Standard- Fräser incl Express- Versand per Amazon Prime 14,95€ gekostet. Dazu habe ich mir noch 2 Stück 0,8 mm Einschneiden- Fräser zu je 4,95€ geleistet, von denen einer bereits abgebrochen ist
… Die Teile oben sind übrigens mit dem Standard- V- Fräser, der im Bausatz enthalten war gefräst. Die V- Fräser sind sehr viel robuster und können auch viel schneller fräsen. Dafür sind die Teile dann nicht ganz so schön wie mit dem dünnen Spezial- Fräser. Hier hat die Genauigkeit aber locker mit dem V- Fräser gereicht. Um auch mal andere Werkzeuge einsetzen zu können, habe ich mir einen kompletten Satz Spannzangen- Einsätze von 1 – 7 mm über Ebay in China gekauft. Die haben incl Aufbewahrungsboxen und Versand 7,95€ gekostet und sind gerade eben eingetroffen. Ausprobieren habe ich sie deswegen noch nicht können.
Dazu sind noch 4 Filzgleiter gekommen, die ich sowieso noch hier liegen hatte (stammen von irgendeinem Diskonter, ich weiß nicht mehr welcher). Unter alle 4 Ecken geklebt reduzieren sie die an den Tisch übertragenden Schwingungen doch sehr deutlich. Damit kann man die Fräse ohne schlechtes Gewissen auch in einer Mietwohnung einsetzte, selbst in der Nacht. In dem Zimmer, in dem die Fräse läuft, kann zwar keiner schlafen, aber das Geräusch ist nicht so laut, das es nebenan stört.
Die Software, die bei mir zum Einsatz kommt, ist kostenlos. Die Treiber und das Steuerprogramm “GRBL-Control” sind im Bausatz enthalten und zum Konstruieren und G-Code erzeugen verwende ich das kostenlose “Carbide Create”, mit dem ich sehr schnell und leicht klar gekommen bin. Es gibt ein alternatives Steuerprogramm (Grbl Controller 3.0) welches ebenfalls kostenlos ist und scheinbar mehr Optionen bietet. Das habe ich bis jetzt aber noch nicht ausprobiert, werde ich demnächst aber tun. Sofern mir die Konstruktionsmöglichkeiten von Carbide Create irgendwann mal nicht mehr ausreichen, so kann man ja jederzeit auch Zeichnungen aus Libre CAD, AutoCad usw importieren und weiter verarbeiten. Zur Zeit sehe ich da aber noch keinen Bedarf.
In der Summe macht das 231,80€ für ein sehr universell einsetzbares und für meine Hobby- Zwecke hervorragendes Werkzeug, das mir unendliche Bastel- Möglichkeiten eröffnet, die ich sonst so nie haben würde. Dazu kommt dann noch “Verbrauchsmaterial” wie Polystyrol- oder Holz- Platten, Doppel- Klebeband und ähnliches.
Der Bau meiner Fräse war auf Grund der unpassenden Muttern ziemlich fummelig und auch nervig. Sieht man davon ab (also sofern man einen Bausatz mit passenden Muttern erwischt) ist der Bau aber von jedem, der weiß, wo die spitze Seite eines Schraubenziehers ist, zu bewerkstelligen.
Die Lernkurve beim CNC Fräsen ist bei weitem nicht so steil wie beim 3D Drucken. Die Zeit vom Anfang bis zu den ersten brauchbaren Ergebnissen ist doch um einiges kürzer. Klar kann man beim Fräsen auch Fehler machen und ich habe garantiert noch längst nicht alle gemacht. Aber im Vergleich zum 3D Drucker sind die Resultate doch deutlich einfacher zu reproduzieren.
Am 3D Drucker muss man obendrein ständig herum basten, hier was umbauen, da was verbessern. Bei der Fräse ist das nicht notwendig, sobald man sie einmal eingerichtet hat.
Das Ergebnis der CNC 3018 ist um einiges besser als bei einem 3D Drucker aus der gleichen Preisklasse (also einem Prusa I3 Klon wie z.B. meinem GEEETech I3 Pro B). Beim 3D Drucker bin ich mir nicht so zu 100% sicher, ob sich die Ausgabe dafür gelohnt hat. Bei der CNC Fräse bin ich es.
Zurück (CNC Fräse Teil 3) – Weiter (CNC Fräse Teil 5)